Unit Leak Test & Unit Test to be performed for Freezer. Performing a unit leak test is crucial for maintaining the efficiency and reliability of freeze dryers in industrial applications. These tests ensure the system’s ability to meet performance standards under specified conditions.
By following detailed procedures, monitoring key parameters, and meeting acceptance criteria, users can ensure optimal functionality and compliance with quality standards. This article provides a step-by-step guide to conducting these tests, including performance benchmarks and troubleshooting tips.
Procedure for Performing a Unit Leak Test and Unit Test
- Start the unit leak test/unit test as per procedure, follow the steps of the cycle, and complete the result table.
- Ensure that chamber door is closed and all valves are in their nominal state
- Ensure that all utility supply is normal, e.g., compressed air, cooling water.
- Â Freeze Dryer is in Auto mode
- Set the performance test parameters as per the table.
- Start the Unit test on SCADA screen, follow the steps listed for the cycle, and
complete the result table.
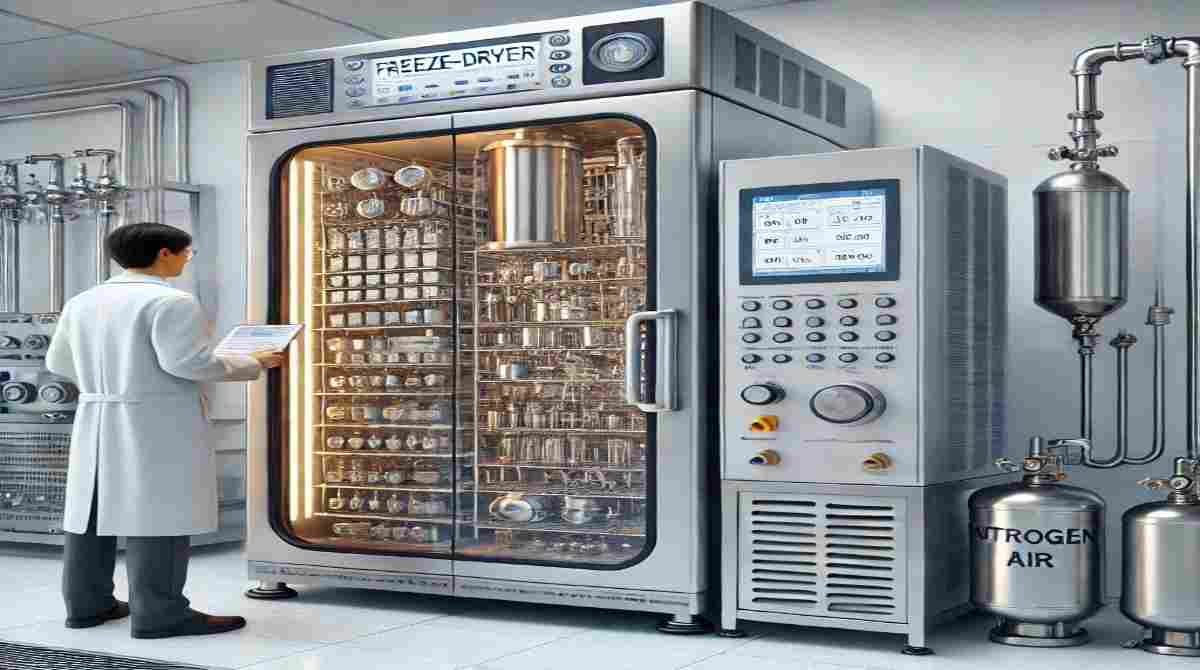