Filter Integrity Test (WIT) Process in Freeze Dryer: Did you know that over 80% of all pharmaceutical and biotechnology products are freeze-dried? This process is key to keeping them stable and free from germs. Testing the filter’s integrity is crucial to ensuring your products are safe and effective.
Learning how to do the filter integrity test (WIT) in your freeze dryer is vital. It helps you follow GMP rules and make products that are top-notch in safety and quality.
Key Takeaways
- Understand the importance of online filter integrity testing in freeze-drying processes
- Discover the role of filters in lyophilization and the consequences of filter failure
- Learn the step-by-step guide to the filter integrity test (WIT) process in freeze dryers
- Ensure your products meet GMP compliance and maintain the highest quality standards
- Protect the sterility and integrity of your pharmaceutical and biotechnology lyophilized product.
- Filter Integrity: A critical element for sterility assurance in biopharmaceutical and vaccine production.
- Testing Timing: Post-use integrity testing is a global regulatory requirement; pre-use testing varies regionally.
- QRM: Required throughout the pharmaceutical process, as per ICH guideline Q9.
- Health, Safety, and Environment (HSE): Regulations aim to control accidents during filter integrity testing.
- Device Compliance: Filter integrity testing devices must meet regulatory expectations for data integrity, QRM, and HSE.
- Sartocheck 5 Plus: Sartorius’ new filter tester complies with industry standards, offering improved ease of use, accuracy, and regulatory compliance.
Understanding the Importance of Filter Integrity Testing in Freeze Drying
In pharmaceutical manufacturing, freeze drying, or lyophilization, is key to keeping drugs potent and stable. At their core, filters keep the environment clean and stop contamination. Testing these filters, known as the filter integrity test (WIT), is vital for freeze drying success.
What Is a Filter Integrity Test?
A filter integrity test is a crucial quality assurance process used to verify that a filtration system is working effectively, ensuring that sterile production environments, particularly in pharmaceuticals and biotechnology, meet the required standards.
This test helps confirm that the filters used are free from damage, leaks, or other issues that could compromise the sterility of the product.
Key Types of Filter Integrity Tests
Bubble Point Test
One of the most common integrity tests, the bubble point test, measures the pressure at which air starts to bubble through a wetted filter. The pressure required correlates with the pore size, ensuring that no larger-than-allowed particles can pass through.
Forward Flow Test
This test measures the flow of gas through a wetted filter under specific pressure conditions, checking whether the filter maintains its integrity without leaks.
Pressure Hold Test
The pressure hold test involves pressurizing the filter, isolating it from the pressure source, and measuring pressure decay over time. Any significant drop in pressure can indicate a compromised filter.
Diffusion Test
The diffusion test measures the rate of gas diffusion through a wetted filter. It checks for small leaks that other tests may miss
The Sartocheck® 5 Plus Filter Tester: A Comprehensive Overview
The Sartocheck® 5 Plus Filter Tester is a state-of-the-art device designed to perform integrity tests on various filtration systems, ranging from small syringe filters to large multi-round housings and tangential flow cassettes. Its automated features, particularly in Quality Risk Management (QRM), ensure that it meets the rigorous standards required in pharmaceutical and biotech industries.
Sartocheck 5 plus alarms
The Sartocheck® 5 Plus features several alarms that enhance operational safety and reliability during filter integrity testing. These alarms alert users to potential issues such as:
- Pressure Alarms: Indicate when pressure levels are outside the acceptable range, signaling possible filter integrity breaches.
- Flow Alarms: Trigger if the flow rate does not meet predefined criteria, which could indicate a clogged or damaged filter.
- System Malfunction Alerts: Notify users of any technical issues with the tester itself, ensuring prompt troubleshooting and maintenance.
These alarm systems help maintain consistent testing quality and compliance with industry standards.
Importance of Filter Integrity Testing
- Quality Assurance: Ensuring filter integrity is critical for maintaining product quality in pharmaceutical and biotech manufacturing. Compromised filters can lead to contamination, affecting the safety and efficacy of products.
- Regulatory Compliance: Many regulatory bodies require routine integrity testing as part of Good Manufacturing Practice (GMP). The Sartocheck® 5 Plus helps organizations comply with these regulations efficiently.
When and Why Is a Filter Integrity Test Necessary?
Pre-use Testing: Before using a filter in a production run, conducting a filter integrity test ensures the filter is in proper working condition and can reliably protect the product.
Post-use Testing: After the production process, a post-use filter integrity test ensures that the filter did not become compromised during operation.
Regulatory Requirements for Filter Integrity Testing
FDA Guidelines
The FDA mandates stringent requirements for filter integrity testing in pharmaceutical and biotech production, ensuring product safety.
- FDA requirement: Filters used in the processing of sterile solutions, such as SVPs and LVPs, must undergo filter integrity testing.
- Documentation: The results of these integrity tests must be included in the batch product records.
Data Integrity
Definition: Data with “integrity” are accurate, free from errors or undocumented edits, attributable (showing who acquired the data), and available for review, audit, or inspection throughout its life cycle.
- Importance in Drug Manufacturing: Filter integrity test results are crucial for releasing final drug products. Ensuring data integrity is not just an IT issue but a significant business risk that can affect drug manufacturing and patient health.
- Regulatory Compliance: The completeness, consistency, and accuracy of data are critical for regulatory compliance in systems that generate, store, and retrieve information. The FDA issued data integrity guidelines in 2016, with an increasing number of warnings related to this issue.
- Protection Against Threats: Malware incidents and the threat of computer viruses highlight the importance of data protection and security.
- New Device Features: The new filter integrity device uses a customized Linux OS, unalterable data formats, and write-protected root-file systems to ensure data integrity and protection from malware and viruses.
The “Four-Eyes Principle” requires that test results be reviewed and approved by at least two individuals. This practice is a key element in quality systems like Good Manufacturing Practices (GMPs), Good Laboratory Practices (GLPs), and ISO standards
Importance of Quality Risk Management in Filter Integrity Testing
- Operator Training: Mandatory for GMP compliance (ICH Q9), reducing errors and improving error detection by QA staff.
- Error Severity Assessment: Necessary to determine required remedial actions for operator errors.
- Quality Risk Management (QRM): Ensures patient safety and is essential for drug lot release.
- Filter Integrity Testing: Critical in drug production; false-passed or false-failed test results can impact patient health, finances, and drug supply.
- Sartocheck 5 Plus Filter Tester: Includes program-specific parameters for filter testing
EU Regulations
Similar to the FDA, the European Union has strict guidelines that regulate the testing and validation of filters in sterile processes.
The Role of Filters in Lyophilization
Filters are crucial in freeze-drying. They block harmful particles or germs that could ruin your pharmaceuticals’ purity. By keeping the lyophilization area clean, filters help keep your products safe and of high quality.
The online filter in the frozen dryer (lyophilization) play a significant role in passing the pure nitrogen into chamber and controlling the microorganism in lyophilized product vials
Consequences of Filter Failure: Impact on Product Quality and Sterility
If a filter fails, the results are bad. It could let in harmful stuff, making your product unsterile or of poor quality. This could mean recalls, breaking rules, and health risks for users. Doing filter integrity tests (WIT) and fixing leak testing issues is key to avoiding these problems.
Knowing how filters work in freeze drying and the need for testing keeps your production safe and follows the rules. It also ensures your products are safe and work well for customers.
Filter integrity test (WIT) process in freeze dryer: A Comprehensive Guide
Keeping filters in a freezer dryer clean and working right is key to keeping products safe and pure. The filter integrity test (WIT) checks how well filters work and if they’re doing their job. It’s a must-do step to make sure everything goes smoothly.
The WIT, or Water Intrusion Test, checks if a filter stops germs from getting through. It’s done before freeze-drying starts and after any filter changes. This test is a standard way to check if filters are working as they should.
- First, get the freezer dryer ready for the test. Make sure the filter is isolated and all connections are tight.
- Then, add a set amount of water to the system. Watch the pressure change across the filter. This change should not go over the filter’s limit, as stated by the maker.
- If the pressure stays within the allowed range, the filter passed the test. This means it’s working right and keeps out bad stuff.
- If the pressure goes too high, it means the filter might be broken. You’ll need to fix it before drying can go on.
Doing the WIT right and understanding the results is key for following GMP rules and keeping products safe. By sticking to these steps, you can trust that your freezer’s filters are doing their best. This keeps your final product safe and pure.
“Proper filter integrity testing is a critical quality control measure that helps protect the sterility and efficacy of freeze-dried pharmaceutical products.”
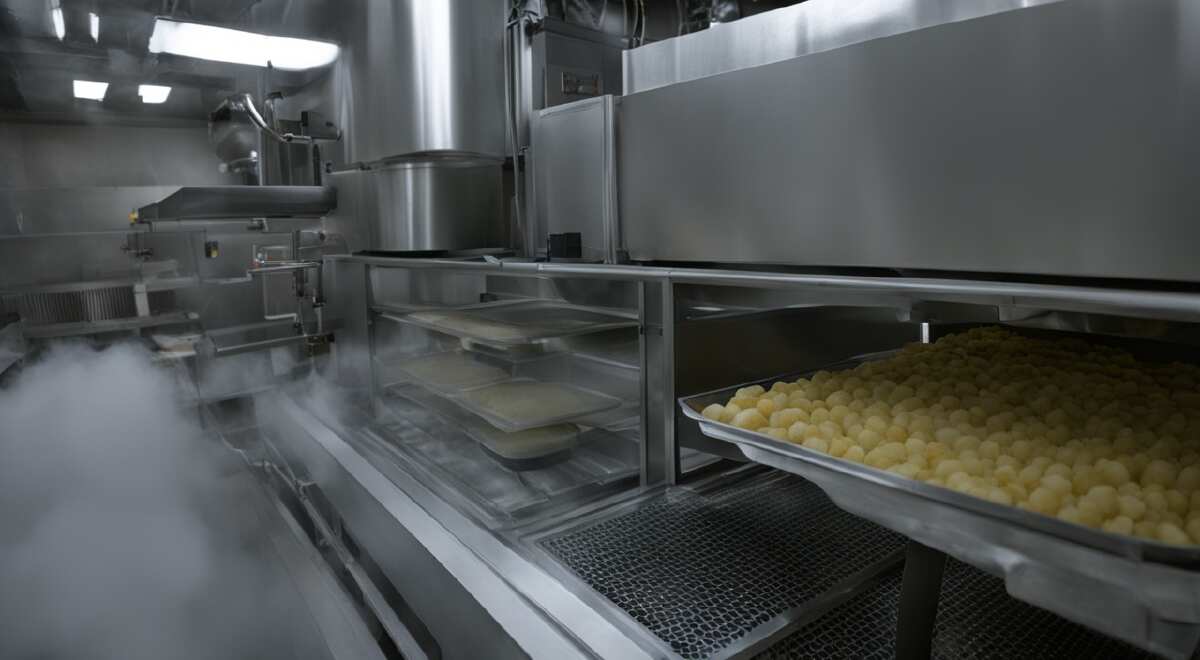
Filter integrity test (WIT) process in freeze dryer
Purpose: The purpose is to check the correct filter integrity test process function
Required documents:
- Document name: test procedureÂ
- List of parameters: list of parameters available for filter integrity testÂ
- Chart-integrity test filter: chart for comparing the parameter
- Batch report: after integrity test report parameter verification
- Functional specification: filter seriol number used during filter integrity test installation in housing of filter
Required instrumentation and auxilary means
- Types of equipment
- Type model/version number
- serial number
- calibration is valid until (up to)
Acceptance criteria: the correct function of the filter integrity test process according to filter integrity chart
Implementation:
- The functional test is based on the process flow chartÂ
- possible instruction and notes in the test documents are to be considered
- The freeze drying unit must be switched on, and all supply media must be connected and present.
- No failure messages, which have an impact on the implementation, are displayed on the SCADA system.
- The tester must be appropriately placed on the freeze-drying unit and the SCADA system
Verification of the integrity test:
The Verification of the integrity test process take place in accordance to the test document required and the related chart available. And between the general parameter and the integrity test parameter. Which are described in documents and start the integrity test process. And compare the state of components (moter, volves, and heating elements) on the chart with the displayed state of documents on the SCADA system. Check all the checked states of components on the chart. The chart and batch report have to be attached to the operational qualification (OQ) documents after testing.
- Acceptance criteria: correct state of components (moter, volves, and heating elements) during the whole integrity test process of the filter run according to the chart.
- Test result: Pass/fail
- Implemented date and signature.
Online filter integrity test parameter in freeze dryer
Set point of filter integrity testÂ
- WIT water temperature: 22.0 °C
- Integrity test pressure: 3600 mbar
- Pemissible pressure drop: 75 mbar
- Maximum test pressure: 3700 mbar
Time duration of filter integrity test
- Maximum time for test pressure: 11 minutes.
- Test pressure stabilization time: 11 minutes.
- Pressure drop test duration: 11 minutes.
- Fitter housing drying time: 11minutes
- Filter cartridge drying time: 16 minutes.
- Cantainer drying time: 6 minutes.
- Cantainer venting times: 2 minutes.
Additional functions of filter integrity test
- Nitrogen: Nitrogen (N2) gas is required during the venting of the filter integrity test.
Fitter data used in filter integrity test in freeze drying
- Filter housing: The housing that encloses filter cartridges bags, or baskets, is called a filter housing. Enter the detailed filter housing serial number (xxxxx, mean Sr.No. of housing used in filter housing).
- Filter cartridges: Inter the filter cartridge number which is used during filter integrity of freeze dryer (AB1PFRXXXX)
- Humidifying medium: Steam condensate The humidifier below is meant to release steam into the surrounding atmosphere via the holes in the panel humidifier tubes. The surfaces are cool because the steam humidifier is in the air stream, and some of the steam heats the metal. As the steam condenses, it escapes through the panel’s bottom. We must now deal with the condensate.
- Testing medium: During the filter integrity test of the freeze dryer, nitrogen was used.
Filter integrity test failure alarm observed:
Test pressure has not built up. Cause of alarm: It is not possible to build up the test pressure. The cause of this failure could be:
- The filter is damaged, and no compressed air to build up the pressure is available
The test pressure is too high. The pressure increased to fast. The test pressure is too high. The cause of this failure could be that the adjustment of compressed air is wrong.
Pressure drops too high: The pressure drop is not within tolerance. The cause of this failure could be: that the filter is damaged
The water temperature in the filter is not stable. The temperature difference of the water in the filter is too high for the filter test. The cause of this failure could be:
- The temperature in the basement is too high
- The start time of the test after SIP was too short
The air temperature is too low. The temperature of the air to dry the filter is too low. The cause of this failure could be:
- No steam is available
- adjustment of steam supply for the heat exchanger is wrong
Conclusion:
Maintaining GMP Compliance and Product Integrity
The filter integrity test (WIT) is key to keeping your pharmaceutical or biotechnology products safe and pure. It helps you meet GMP standards and keep your products top-notch. This test ensures your products are clean and safe for customers.
We’ve looked at how filters are crucial in freeze drying and what happens if they fail. We’ve given you a detailed guide on how to do the WIT test correctly. This will help you keep your products up to standard.
Keeping up with GMP and ensuring product quality is vital for your business’s success. By focusing on the filter integrity test (WIT) in freeze drying, you show you care about quality.Â
FAQ
What is the filter integrity test (WIT) process in a freeze dryer?
The filter integrity test (WIT) in a freeze dryer checks if the filters work right. It makes sure the filters keep the products clean and safe. This test stops bad stuff from getting into the products, keeping everything pure.
Why is the filter integrity test (WIT) important in freeze drying?
The WIT is key because it keeps the freeze-drying area clean. If the filters don’t work, the product can get dirty and not work right. This test makes sure the filters are good, keeping the freeze drying safe and clean.
What are the steps in the integrity test (WIT) process for a freeze dryer?
The WIT process for a freezer dryer has a few steps: 1. Get the freeze dryer and WIT gear ready. 2. Do the WIT test by putting pressure on the filters or testing their bubble point. 3. Watch how the filters react and check the results to make sure they’re okay. 4. Write down the test results and keep them for quality checks and rules.
How does the filter integrity test (WIT) help maintain GMP compliance in pharmaceutical and biotechnology processes?
The WIT is a big part of following Good Manufacturing Practices (GMP) in making medicines and biotech products. It makes sure the filters in freeze drying work right. This keeps the products clean and safe, which is important for rules and keeping patients safe. Doing the WIT well shows a strong focus on quality and following GMP rules.
What are the consequences of filter failure in a freezer dryer?
If freeze dryer filters fail, it’s bad news for the product’s quality and cleanliness. This can lead to: dirty products and loss of cleanliness changes in the product’s makeup; more risks for patient safety, especially with injectables Trouble with rules and possible recalls big losses for the company’s image and money