Failure Detection and Elimination Fuse Failure (Circuit breaker) during lyophilization. Did you know that over 80% of all food production uses lyophilization, or freeze-drying? This method is key to preserving food and is worth $54 billion globally. But the electrical systems that power these units face a big risk: fuse failure. A blown fuse can stop production, causing big losses and safety issues.
We’re going to look into how lyophilization works and how to spot and prevent fuse failures. By understanding this, food and pharmaceutical companies can keep their operations safe and efficient. This ensures their lyophilization equipment works well and safely.
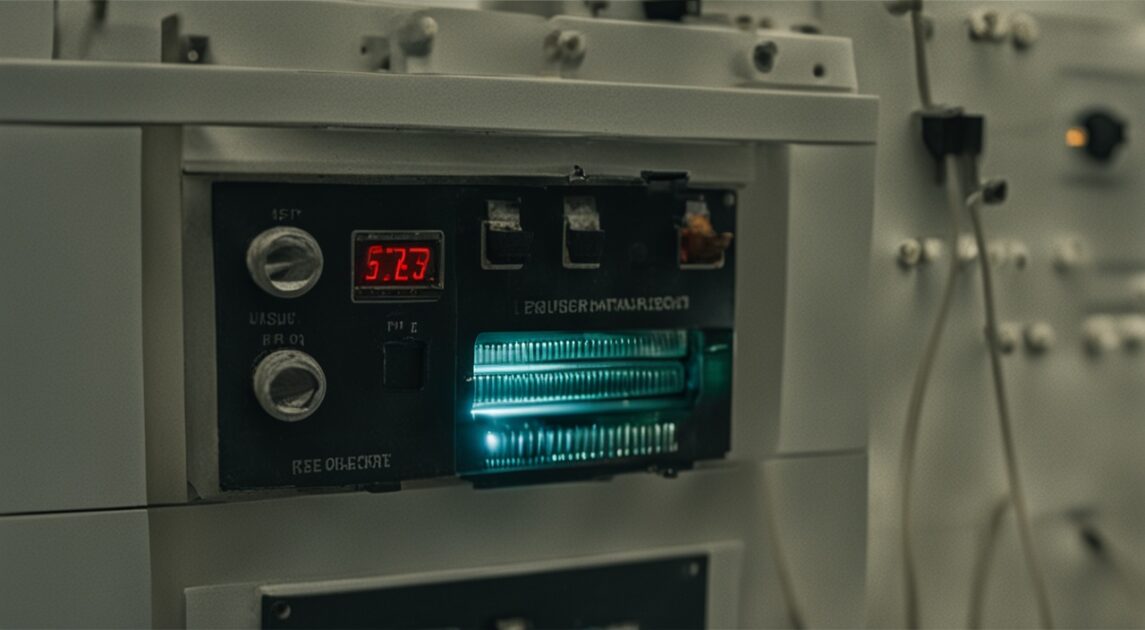
Key Takeaways
- Lyophilization, or freeze-drying, is a critical dehydration process used in over 80% of food production facilities
- Fuse failures in lyophilization circuits can disrupt production and compromise product quality
- Understanding the causes of fuse failure, including electrical overload and thermal stress, is essential for preventive maintenance
- Proper circuit design, regular inspections, and advanced monitoring techniques can help detect and eliminate fuse failures
- Safeguarding lyophilization equipment is crucial for the $54 billion global food preservation industry
Understanding Lyophilization and Its Importance
Lyophilization, also known as freeze-drying, changes how we store and transport food. It removes moisture from materials by turning frozen water into gas without going through liquid. This keeps the food’s original taste, structure, and nutrients, making it crucial in many fields.
What is lyophilization?
Lyophilization freezes a product and then takes out water through sublimation. It’s great for keeping things like medicines, biological samples, and food safe. This method maintains the product’s quality and structure, making it last longer.
Applications of Lyophilization
- Food preservation: It’s used in the food industry to keep fresh produce, dairy, and baked goods fresh for longer. It maintains vitamin protien and their nutrients and taste.
- Pharmaceutical and medical industries: Important for storing and moving sensitive drugs, vaccines, and biological samples. It keeps them potent and effective.
Scientific research: Helps preserve delicate samples like DNA (deoxyribonuclic acid), enzymes (all amino acids are protien), and cells for research.
- Aerospace and military applications: Freeze-dried foods are used in space missions and military operations. They’re light, compact, and last a long time, providing food in tough places.
Lyophilization has changed how we keep food, store medicines, and do research. It uses sublimation to keep materials safe without losing their quality. This makes it key in many industries.
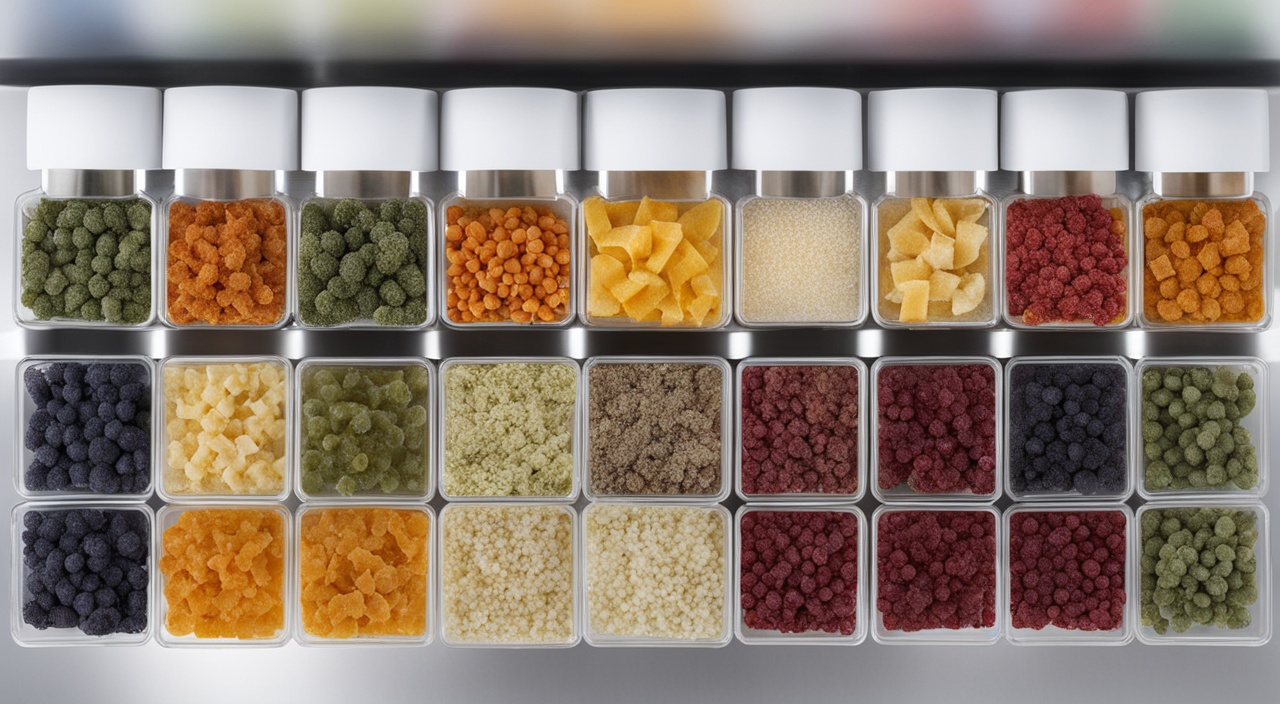
Failure Detection and Elimination: Fuse Failure (Circuit Breaker) during Lyophilization
In the pharmaceutical world, keeping the lyophilization stage safe is key. If fuses or circuit breakers fail, it can mess up the temperature, pressure, and airflow needed for drying. This can cause product loss, damage to equipment, and safety risks.
It’s vital to have good failure detection and elimination plans for lyophilization. Knowing why fuses fail and circuit breakers trip helps manufacturers take steps to stop these problems before they start.
Identifying the Causes of Fuse Failure
There are two main reasons why fuses or circuit breakers might fail during lyophilization:
- Electrical Overload: If there’s a sudden jump in electrical current, like from a machine breaking down or a power surge, it can overload the circuit. This might make the fuse blow or the circuit breaker trip.
- Thermal Stress: High temperatures for a long time can wear out the fuse or circuit breaker parts. This makes them more likely to fail during drying.
Cause | Impact | Preventive Measures |
---|---|---|
Electrical Overload | Sudden spikes in electrical current can overload the circuit and lead to fuse failure or circuit breaker trips. | Proper circuit design and installation, regular equipment maintenance, and the use of surge protection devices. |
Thermal Stress | Extreme temperatures and prolonged exposure to heat can cause the fuse or circuit breaker components to degrade, increasing the risk of failure. | Implementing effective cooling systems, ensuring adequate ventilation, and regularly inspecting and replacing critical components. |
By fixing these issues and taking steps to prevent electrical faults, pharmaceutical companies can make their lyophilization safer and more reliable. This reduces the chance of current overload protection failures.
Fuse Failure (Circuit Breaker)
Description: Fuse failure, or circuit breaker tripping, occurs when a fuse has been activated due to a short circuit. This failure halts the electrical supply to critical components, potentially affecting the freeze-drying process.
Solution:
- Identify the Short Circuit: Check for any visible signs of damage or malfunction in the wiring and connections. Inspect the circuit for any short circuits and rectify them.
- Replace the Fuse: Replace the blown fuse with a new one of the same rating. Ensure that the new fuse is properly installed.
- Prevent Future Failures: Regularly inspect and maintain electrical components to prevent recurrence. Ensure that the system is not overloaded and that all connections are secure.
Fuse Failure (Circuit Breaker): This failure appears if a fuse has been released. The cause of this failure is a short circuit.
Emergency power is active
Description: When a power failure occurs, the system automatically switches to an emergency power supply. During this phase, only the essential freeze-drying programs necessary to protect the product are run.
Solution:
- Monitor Emergency Power Activation: Ensure that the emergency power supply is functioning correctly and that it supports all critical functions.
- Verify Program Operation: Check that the freeze-drying programs are operating as required and that the product protection measures are in place.
Emergency power active: If there is a power failure, the system switches over to the emergency power supply, i.e. the freeze-drying programs are run only with the machines that are necessary to protect the product
Emergency off active:
Description: The emergency off button has been pressed, resulting in the disconnection of power to the outputs. This action is typically taken in response to a critical issue requiring immediate shutdown.
Solution:
- Check Emergency Off Button: Verify that the emergency off button has been released or unclamped. Ensure it is not engaged unintentionally.
- Restore Power: Press one of the control buttons to restore power. Confirm that all systems return to normal operation.
An operator pressed the emergency off button. The power of the outputs is switched off. Check the emergency off They have to be unclamped. Push one of the control on buttons.
Main Power Restored
Description: This alarm message indicates that power has been restored after an outage. It confirms that the main power supply has been reactivated.
Solution:
- Verify Power Restoration: Check that the main power supply is stable and that all systems are operating correctly after the restoration.
- Inspect System Functionality: Ensure that all freeze-drying processes are functioning as intended and that no residual issues remain from the power outage.
Main Power Restored: This alarm message appears if, after a power failure, the main power was restored. Voltage too low: The voltage of the power supply is too low. This alarm message appears if the voltage control relay for the main power supply gives an alarm.
Voltage Too Low
Description: A low voltage alarm indicates that the power supply voltage is below the acceptable level. This can be triggered by the voltage control relay for the main power supply.
Solution:
- Check Voltage Levels: Use a voltmeter to measure the power supply voltage. Compare it with the required voltage specifications.
- Investigate Causes: Determine if there are any issues with the power supply or if there is a need for voltage regulation. Address any electrical faults that may be causing the low voltage.
- Consult with an electrician. If the problem is not solved, then consult with professional assistance to diagnose and resolve the problem.
Voltage of the power supply too low. This alarm message appears, if the voltage control relay for the main power supply gives an alarm
Conclusion
Effective failure detection and elimination are essential for maintaining the reliability of lyophilization equipment. By understanding and addressing issues related to fuse failure, emergency power activation, emergency off scenarios, power restoration, and low voltage, you can ensure a smooth and uninterrupted lyophilization process.Â
FAQ
What is the difference between freeze dryers and dehydrators?
Freeze dryers and dehydrators are both the same But they do it in different ways. Freeze dryers freeze food and then remove moisture by reducing pressure. This makes the frozen water turn directly into vapor. Dehydrators, however, use warm, dry air to make the water in food evaporate.
What are the main causes of fuse failure in lyophilization circuits?
Fuses often fail due to two main reasons in lyophilization circuits. The first is when the system draws too much current, causing the fuse to blow. The second is when the extreme temperature changes in the process wear out the fuse over time.
What are some preventive measures to address fuse failure in lyophilization circuits?
To stop fuses from failing, you can take a few steps. First, check and maintain the electrical parts often. This includes fuses, circuit breakers, and more. Second, make sure the circuit design and the placement of fuses are right for the lyophilization process.
What are the failures of lyophilization?
Failures in lyophilization can arise from several issues, including improper packaging, incorrect temperature and pressure settings, errors in the lyophilization cycle, using unsuitable equipment, inadequate cleaning and sterilization, and an improper storage environment