The purpose of this Lyophilizer Operational Qualification(OQ) is to provide documented evidence that the functions of the freeze drying unit adhere to the appropriate codes and approved design intentions and current Good Manufacturing and Engineering Practice.
Lyophilization, or freeze-drying, is a critical process in industries like pharmaceuticals and biotechnology. Ensuring that a lyophilizer operates correctly is vital for product quality and process reliability. This is where Operational Qualification (OQ) comes into play. In this article, we’ll dive deep into the lyophilizer operational qualification process, outlining its importance, steps, and best practices.
What is a Lyophilizer?
A lyophilizer, commonly known as a freeze-dryer, is a device used to remove moisture from a product after it is frozen. This process, known as lyophilization, is essential in industries like pharmaceuticals, where the stability and shelf life of a product are critical. The lyophilizer works by lowering the pressure and applying heat to allow the frozen water in the product to sublimate directly from the solid phase to the gas phase.For those encountering issues like pressure deviations in lyophilizers, you may refer to our troubleshooting guide for pressure deviation issues to address these challenges effectively.
Understanding Operational Qualification (OQ)
Operational Qualification (OQ) is a critical phase in the validation of any equipment, including lyophilizers. It involves testing and verifying that the lyophilizer operates according to its designed operational specifications. OQ is typically conducted after Installation Qualification (IQ), which ensures that the equipment has been installed correctly.
The OQ provides documented evidence that the system performs as intended throughout all anticipated operating ranges. It contains the procedures to verify specific dynamic attributes of a system or piece of equipment throughout its operating range, which may include “worst case” conditions. Completion of the OQ and sign off .Confirms conformity with the design specifications and authorizes the start of Performance Qualification (PQ).
Scope :This report covers the Operational Qualification (0Q) of the processes, sequences and all control systems (PLC and PC) related functions of Freeze Drying Unit. Testing will be executed by qualified engineers
Responsibility
- Verify that the system is properly operating
- Write the protocol
- Execute the tests
- Document and resolve deviations
- Write OQ Summary Report
- Approve the protocol
- Review OQ test result
- Review and approve OQ Summary Report
OQ FAT, SAT and Commissioning report
 Freeze dryer internal testing and commissioning phase will be performed prior to FAT. This includes a comprehensive testing of the system functionality. In general the tests will only be documented for internal use.
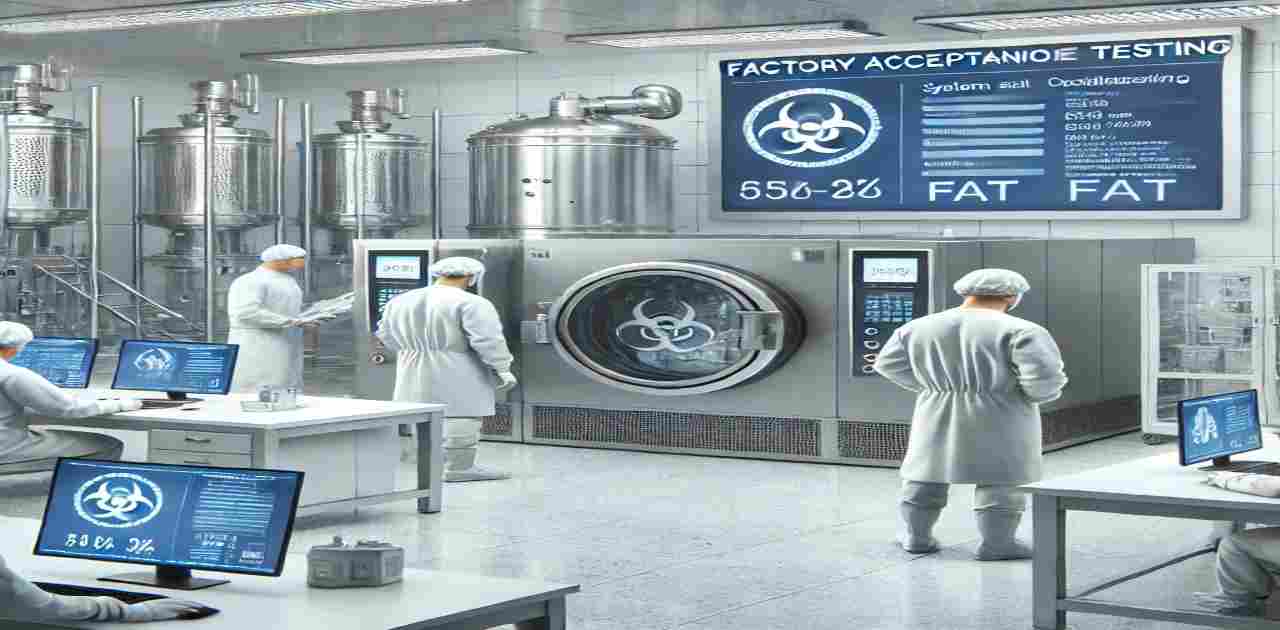
To reduce test time and project lead time it is suggested to combine the commissioning tests and the IQ tests as far as possible to avoid redundant testing.
Tests which are related to the design and will not affect by the disassembly of the equipment (e.g. password test, operator error, condenser capacity) relevant tests have to be commonly agreed during FAT.
Summary Report: This conclusion provides an overview and summary of all OQ activities. It will included a list of deviations,
Acceptance Criteria
- Â All test procedures must be successfully completed.
- Â All acceptance criteria for individual tests are considered acceptable.
- Â All attachments to the OQ tests must be complete and enclosed.
- An observation report must be issued whenever the acceptance criteria are not fulfilled.
- All observation reports must be closed. If observation reports remain open at the end of OQ testing it has to be stated and an evaluation of whether PQ) may start or not must be done.
Operational Qualification Overview
All Electrical Tests result pass
- Functional Test of the Freeze Drying Process and Stoppering SystemÂ
- Functional Test of the Defrosting Process
- Functional Test of the Sterilization (SIP) Process
- Functional Test of the Clean in Place (CIP) Process
- Functional Test of the Filter Integrity Test (WIT) Process.
- Functional Test of the Media Fill Process
- Functional Test of Process and Failure Messages
- Functional Test of the Door Opening System
- Check the System against Operation Error
- Functional Test of Password Protection
- Verification of Audit trial Functionality
- Verification Screen Layouts
- Verification of Batch Report
Importance of OQ in Lyophilization
OQ is vital in lyophilization as it ensures that the equipment can consistently perform under the specified conditions required for the process. Without a thorough OQ, there’s a risk of product failures, leading to potential financial losses and, more importantly, compromised product safety and efficacy.
Key Components of Lyophilizer OQ
Installation Qualification (IQ) vs. Operational Qualification (OQ)
While IQ focuses on verifying that the lyophilizer is installed correctly and according to manufacturer specifications, OQ takes it a step further by validating that the equipment functions within the operational parameters necessary for freeze-drying processes.
Equipment Calibration and Validation
Calibration and validation of equipment are foundational to a successful OQ. Ensuring that all measurement devices on the lyophilizer, such as temperature sensors and pressure transducers, are accurately calibrated is crucial.
Temperature Sensors
Temperature sensors must be calibrated to ensure they provide accurate readings. This is essential for maintaining the precise temperature conditions required during the lyophilization process.
Pressure Transducers
Pressure transducers must also be validated to ensure they can accurately measure the pressure within the lyophilizer chamber. Proper pressure control is critical for effective sublimation during freeze-drying.
Defining Operational Parameters
Establishing clear operational parameters is a key component of OQ. These parameters include:
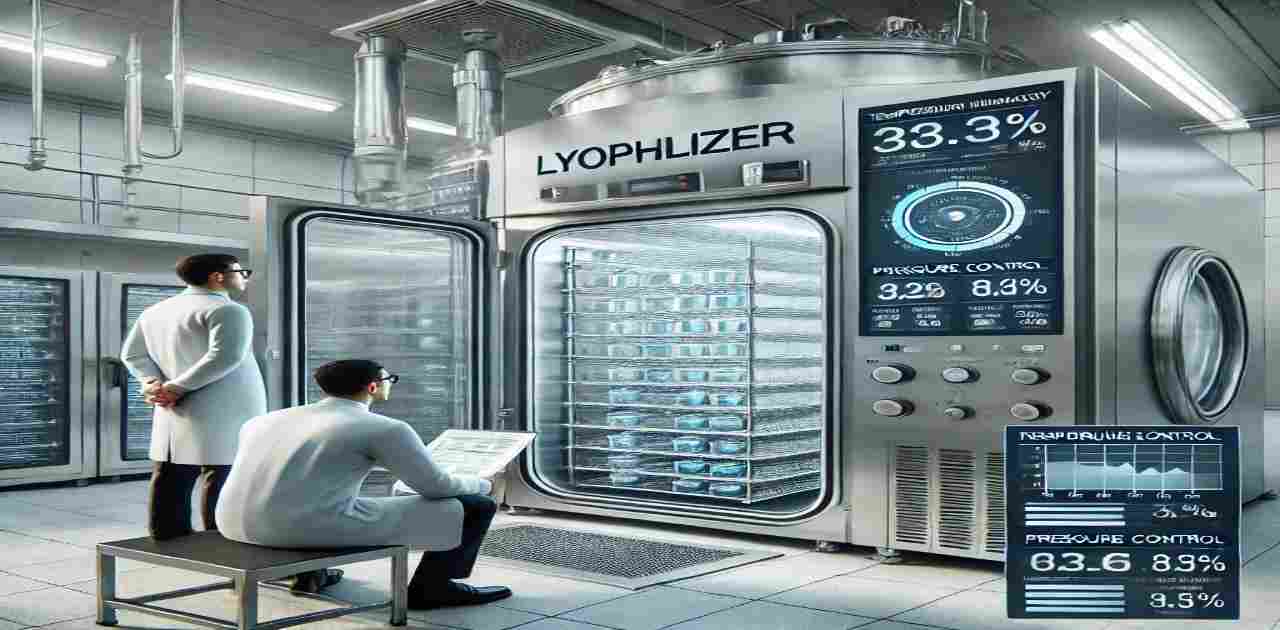
Temperature Uniformity: Ensuring uniform temperature distribution across the lyophilizer shelves is vital to prevent product degradation and ensure consistent drying.
Pressure Control: Stable pressure control is essential for the lyophilization process, as pressure fluctuations can affect the rate of sublimation and product quality.
Shelf and Chamber Performance: The performance of the lyophilizer shelves and chamber must be evaluated to ensure they can maintain the necessary conditions throughout the freeze-drying process.
Steps to Conduct Lyophilizer OQ
Pre-OQ Preparations
Before conducting OQ, thorough preparation is essential. This includes developing detailed protocols and ensuring that all personnel involved are adequately trained.
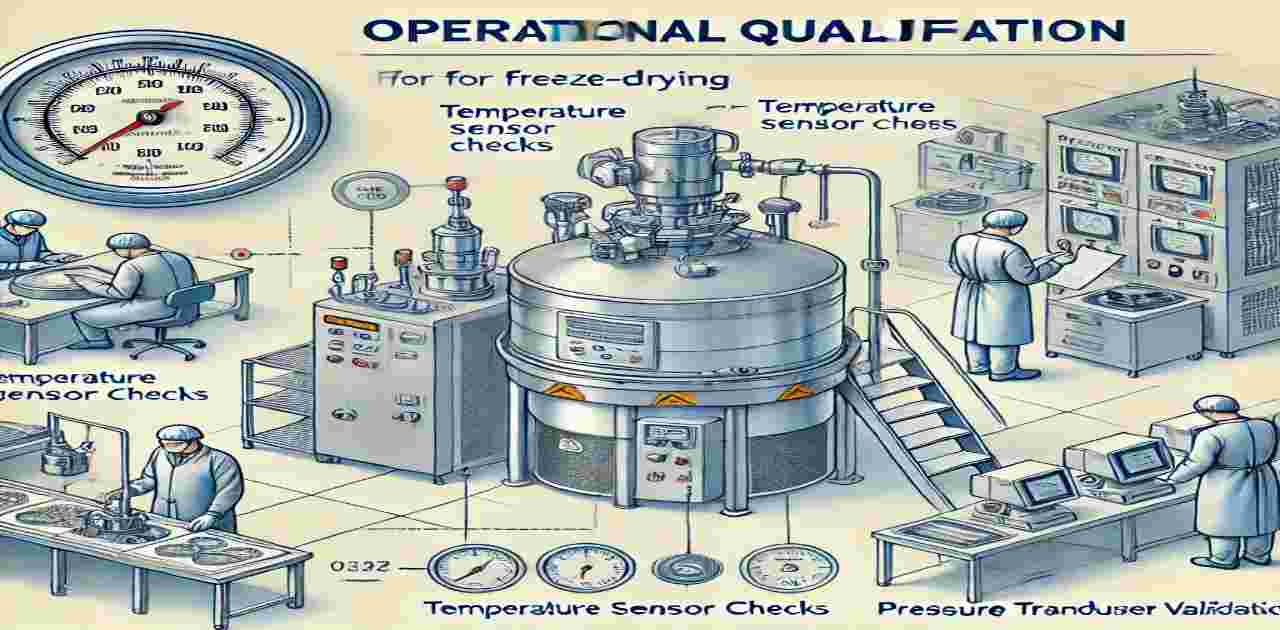
Documentation and Protocol Development
Detailed documentation and protocol development are the backbones of a successful OQ. These documents should outline the specific tests to be conducted, the acceptance criteria, and the procedures for data collection and analysis.
Training of Personnel
Personnel involved in the OQ process must be trained on the equipment and the specific protocols to ensure accurate and reliable testing.
Execution of OQ Protocol
Executing the OQ protocol involves conducting a series of tests to verify the lyophilizer’s performance under both empty and loaded conditions.
Testing Under Empty and Loaded Conditions
Testing the lyophilizer under both empty and loaded conditions is crucial to evaluating its performance. Empty condition tests help in identifying baseline operational capabilities, while loaded condition tests ensure that the lyophilizer can handle actual production scenarios.
Environmental Monitoring
Monitoring environmental conditions such as room temperature and humidity is essential during OQ to ensure that external factors do not affect the results.
Data Collection and Analysis
Accurate data collection and thorough analysis are critical during OQ. The data collected should be compared against the predefined acceptance criteria to determine if the lyophilizer operates within the required parameters.
Post-OQ Activities
After completing the OQ testing, several activities must be performed to finalize the qualification process.
Report Generation: A comprehensive report should be generated, documenting all the tests conducted, the results obtained, and any deviations from the expected performance.
Addressing Deviations: If any deviations are identified during the OQ process, they must be addressed and resolved. This may involve recalibrating equipment, revising operational parameters, or conducting additional tests.
Approval and Documentation: Once all deviations have been addressed, the OQ results must be reviewed and approved by the relevant authorities. Proper documentation of the entire process is essential for regulatory compliance.
Common Challenges in Lyophilizer Operational Qualification
Temperature Variability: One of the most common challenges in lyophilizer OQ is temperature variability across the shelves. Inconsistent temperatures can lead to uneven drying and affect product quality.
Pressure Fluctuations: Pressure control is critical during lyophilization, and fluctuations can compromise the sublimation process. Identifying and mitigating pressure-related issues is crucial during OQ.
Equipment Malfunctions: Malfunctions of the lyophilizer or its components during OQ can lead to delays and require additional testing. Regular maintenance and pre-OQ checks can help minimize these issues.
Best Practices for Successful Lyophilizer OQ
Regular Calibration and Maintenance: To ensure ongoing reliability, regular calibration and maintenance of the lyophilizer and its components are essential. This helps in maintaining the accuracy of the equipment and reduces the risk of deviations during OQ.
Comprehensive Documentation: Thorough documentation throughout the OQ process is vital for ensuring that all aspects of the lyophilizer’s operation are covered and for meeting regulatory requirements.
Continuous Training and Development: Ongoing training for personnel involved in lyophilizer operations and OQ is important to keep them updated on best practices, new technologies, and any changes in regulatory requirements.
Conclusion of Lyophilizer Operational QualificationÂ
Lyophilizer Operational Qualification (OQ) is a critical process in ensuring that freeze-drying equipment operates reliably and effectively. By following a structured approach to OQ, including thorough preparation, execution, and documentation, organizations can ensure the quality and safety of their lyophilized products. Regular calibration, addressing common challenges, and adhering to best practices will further enhance the success of the OQ process.
FAQs on Lyophilizer Operational Qualification (OQ)
What is Operational Qualification (OQ) in lyophilization?
Operational Qualification (OQ) is a critical phase in the validation process of a lyophilizer, where the equipment is tested to ensure it operates within specified parameters required for freeze-drying processes. It involves verifying the functionality of key components like temperature sensors, pressure transducers, and operational controls.
Why is OQ important in lyophilization?
OQ ensures the lyophilizer operates consistently under the defined conditions necessary for effective freeze-drying. It helps prevent product failures, ensures quality and safety, and complies with regulatory standards, ultimately reducing financial risks and improving reliability.
What are the key steps in conducting lyophilizer OQ?
- Preparing detailed protocols and documentation
- Calibrating and validating equipment, including temperature sensors and pressure transducers
- Testing operational parameters like temperature uniformity, pressure control, and shelf performance
- Training personnel involved in the process
- Compiling and reviewing OQ results and issuing a summary report
How do temperature uniformity and pressure control affect lyophilization?
Temperature uniformity ensures even drying across all shelves, preventing product degradation. Stable pressure control is critical for effective sublimation during freeze-drying, as pressure fluctuations can lead to inconsistent product quality.
What is the difference between Installation Qualification (IQ) and Operational Qualification (OQ)?
IQ focuses on verifying the proper installation of the lyophilizer according to design specifications, while OQ validates that the equipment functions correctly within its operational parameters to meet freeze-drying requirements.
Internal Link:
Troubleshooting guide for pressure deviation issues
Link: https://asitafreezedryer.com/troubleshooting-failure-condenser-cooling-issues/