Test of freeze dryer CIP Process Efficiency is the Clean-in-Place (CIP) process is an essential procedure in maintaining the hygiene and operational efficiency of freeze dryers. This test aims to evaluate the effectiveness of the CIP process by verifying its ability to remove riboflavin/B2-vitamin residues from the freeze-drying chamber and internal surfaces. A well-executed CIP process ensures compliance with industry hygiene standards, prevents cross-contamination, and enhances the longevity of freeze-drying equipment.
Purpose freeze dryer CIP Process Efficiency
The purpose of this test is to evaluate the efficiency of the Clean-In-Place (CIP) process in a freeze dryer to ensure thorough cleaning and compliance with regulatory requirements.
Test Documents
- Document Name
- Document Number
- Version Number
- Number of Pages
Test Documents of Freeze dryer CIP Process Efficiency
The Test Documents section provides essential details about the documents used to validate the efficiency of the Clean-In-Place (CIP) process in a freeze dryer. These documents serve as official records and must be accurately maintained for compliance, traceability, and quality assurance.
1. Document Name
This refers to the title or name of the test document that describes the procedure, requirements, and acceptance criteria for the CIP efficiency test. It helps identify the document’s purpose and content at a glance.
2. Document Number
Each test document is assigned a unique document number for tracking and reference. This number ensures that the correct version of the document is used and avoids confusion with outdated or incorrect procedures.
3. Version Number
The version number indicates the specific revision of the document. Since test procedures may be updated over time due to new regulations, technological improvements, or process refinements, version control ensures that only the latest and most accurate document is followed.
4. Number of Pages
This specifies the total number of pages in the document. If the field is blank, it implies that additional supporting documents must be attached to complete the qualification process.
Purpose of This Section
Proper documentation helps maintain regulatory compliance, process standardization, and data integrity. It ensures that all necessary information is available for review during audits, inspections, and quality control assessments
List of Parameters: LXXX-001AB
Note: If the “Number of Pages” column is blank, all relevant documents contributing to the test result must be attached to the qualification binder. Ensure that all test documents are marked, and the first page is stamped as a “Qualification Document.”
Required Instrumentation and Auxiliary Means
This section outlines the necessary tools, equipment, and supporting materials required to conduct the Clean-In-Place (CIP) process efficiency test in a freeze dryer. Each listed item plays a crucial role in ensuring accurate testing and validation.
1. Type of Equipment
This refers to the specific machinery or tools used in the CIP process, such as the freeze dryer unit, spray nozzles, or automated cleaning systems. The equipment must be appropriate for the test and function correctly.
2. Type, Model/Version Number
The specific model or version of the equipment being used must be recorded to ensure consistency in testing. This information helps track changes, compare performance over time, and comply with regulatory documentation requirements.
3. Serial Number
The unique identifier assigned to each piece of equipment. Recording the serial number ensures traceability and accountability in case of performance issues or future inspections.
4. Valid Until
Some instruments or auxiliary means, such as UV lights or riboflavin solutions, may have an expiration date or a recommended validity period. Ensuring that all materials used are within their valid period guarantees the reliability of test results.
5. Riboflavin/B2 Vitamin
Riboflavin (Vitamin B2) is used as a fluorescent tracer in CIP efficiency testing. When exposed to UV light, riboflavin glows, allowing testers to visually inspect areas that have been effectively cleaned. Any remaining traces indicate insufficient cleaning.
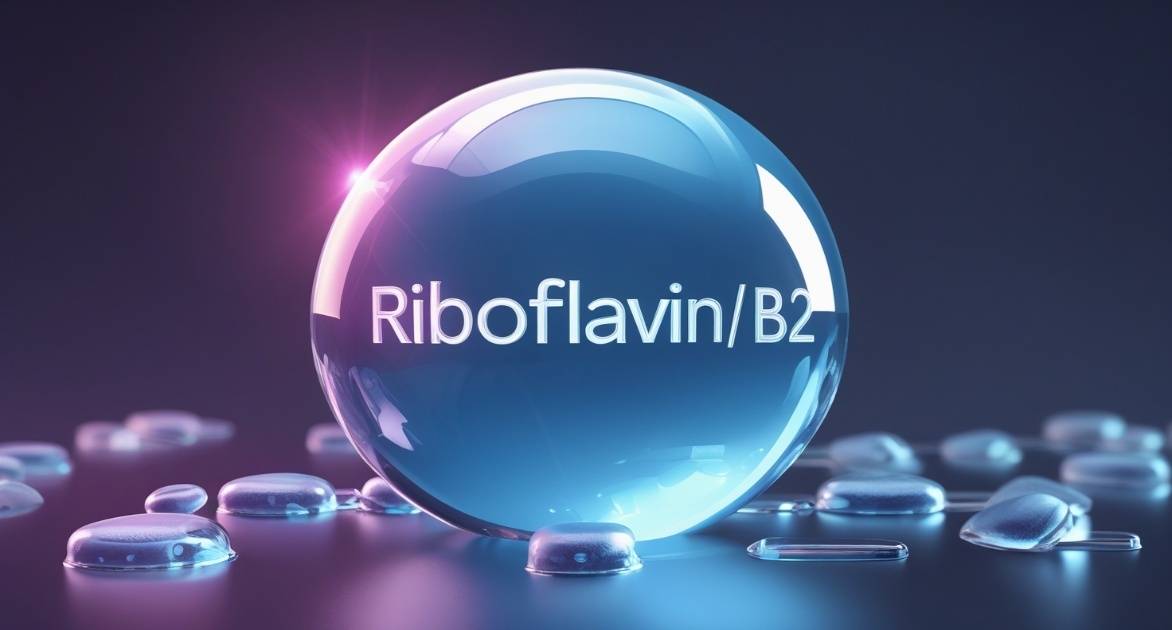
6. UV Light
Ultraviolet (UV) light is used to detect riboflavin residues. The UV light causes riboflavin to fluoresce, making it easier to identify areas where the cleaning process may have been incomplete.
Purpose of This Section
By ensuring that all required instrumentation and auxiliary means are available and properly documented, the CIP process can be validated effectively, ensuring a high standard of cleanliness and compliance with industry regulations.
Acceptance Criteria: A visual inspection under UV light must confirm that the entire interior is sprayed with riboflavin/B2 vitamin. Any traces of riboflavin should not exceed 4% of the total surface area.
Implementation
- Follow all instructions provided in the test documents.
- The freeze-drying unit must be switched on, with all supply media connected and functioning.
- No failure messages that could impact the process should be displayed on the SCADA system.
- The assigned tester must be appropriately authorized to access the freeze-drying unit and SCADA system.
For insights into freeze dryer periodic performance verification, refer to this guide.
Performance of Test
The verification of CIP efficiency follows the procedure outlined in LOEE1507-001A-1.
Step 1: Pre-CIP Riboflavin Application
- Open the freezer dryer chamber door.
- Spray a maximum of 3000 ml of water containing 0.5 g riboflavin/B2 vitamin per liter onto the entire interior surface using a spray bottle.
Acceptance Criteria: A visual check with UV light must confirm that all shelves are adequately sprayed with riboflavin/B2 vitamin.
Step 2: Drying Process
- Leave the chamber door open.
- Initiate manual shelf heating to evaporate water from the solution.
- Heat the shelves to 40°C for approximately 120 minutes.
For further details on temperature control in freeze-drying processes, visit this resource.
Step 3: CIP Process Execution
- Once the riboflavin solution has dried, enter the CIP process ID LOT1507-001C-1 and initiate the CIP cycle.
- Upon completion of the CIP process, perform a UV light inspection to assess cleaning efficiency.
- Document any detected riboflavin traces in the provided table.
- Properly describe and locate the affected areas for further cleaning validation.
- Estimate the affected area and calculate the ratio against the total surface area.
For understanding lyophilizer cleaning validation, refer to this article.
Acceptance Criteria
- The trace amount of riboflavin should not exceed 1% of the total surface area.
- If contamination exceeds the limit, additional cleaning and validation procedures must be performed.
For insights into refrigeration compressor failures in freeze-drying processes, check this guide.
By following these procedures, the efficiency of the freeze dryer CIP process can be verified and maintained to ensure compliance with quality and regulatory standards.
Acceptance criteria: trace amount of riboflavin do not exceed 1% of total surface area
Summary
The efficiency of the freeze dryer CIP process is assessed using riboflavin/B2-vitamin as a tracer and UV light for detection. The test involves spraying the freezer’s interior with a riboflavin solution before initiating the CIP cycle. After the process, a visual inspection under UV light determines whether any traces of riboflavin remain. Acceptance criteria require that riboflavin residues do not exceed 1% of the total surface area. Any remaining traces are documented for further cleaning validation. Compliance with these criteria confirms the effectiveness of the CIP process.
Conclusion
A properly functioning CIP system is crucial for maintaining hygiene and efficiency in freeze-drying operations. The test results indicate whether the cleaning process effectively removes riboflavin/B2-vitamin residues, ensuring compliance with industry standards. If riboflavin traces exceed the acceptable limit, further validation and optimization of the CIP process are required. By following this procedure, manufacturers can uphold stringent cleanliness standards and improve equipment reliability.
FAQs OF Freeze dryer CIP Process Efficiency
1. What is the purpose of testing the freeze dryer CIP process?
The test evaluates the efficiency of the CIP process in cleaning the freezer’s interior by ensuring that riboflavin/B2-vitamin residues are removed effectively.
2. What equipment and materials are required for this test?
The test requires a freeze dryer, riboflavin/B2-vitamin solution, a spray bottle, UV light, and a SCADA system for monitoring the process.
3. How is the test performed?
The test involves spraying the interior of the freeze dryer with a riboflavin/B2-vitamin solution, drying it, running the CIP process, and inspecting the surfaces with UV light for any remaining traces.
4. What are the acceptance criteria for the CIP process?
The cleaning process is considered successful if riboflavin residues do not exceed 1% of the total surface area after cleaning.
5. What happens if the CIP process fails to meet the acceptance criteria?
If riboflavin traces exceed the limit, additional cleaning validation and process optimization are required to ensure effective cleaning.