Did you know that nearly 1 in 4 freeze dryer makers worldwide faced a hydraulic system failure last year? These issues can cause big problems in making freeze-dried products, leading to millions of dollars lost in productivity and product quality. It’s important to know why these failures happen and how to fix them to keep freeze dryers working well.
This article will look closely at hydraulic systems in freeze dryers. We’ll see how they’re key to making freeze-dried foods and what happens if they fail. We’ll cover the main reasons for these failures, like pump and valve problems, temperature issues, and vacuum sealing troubles. Plus, we’ll share tips on how to prevent these problems and fix them if they happen.
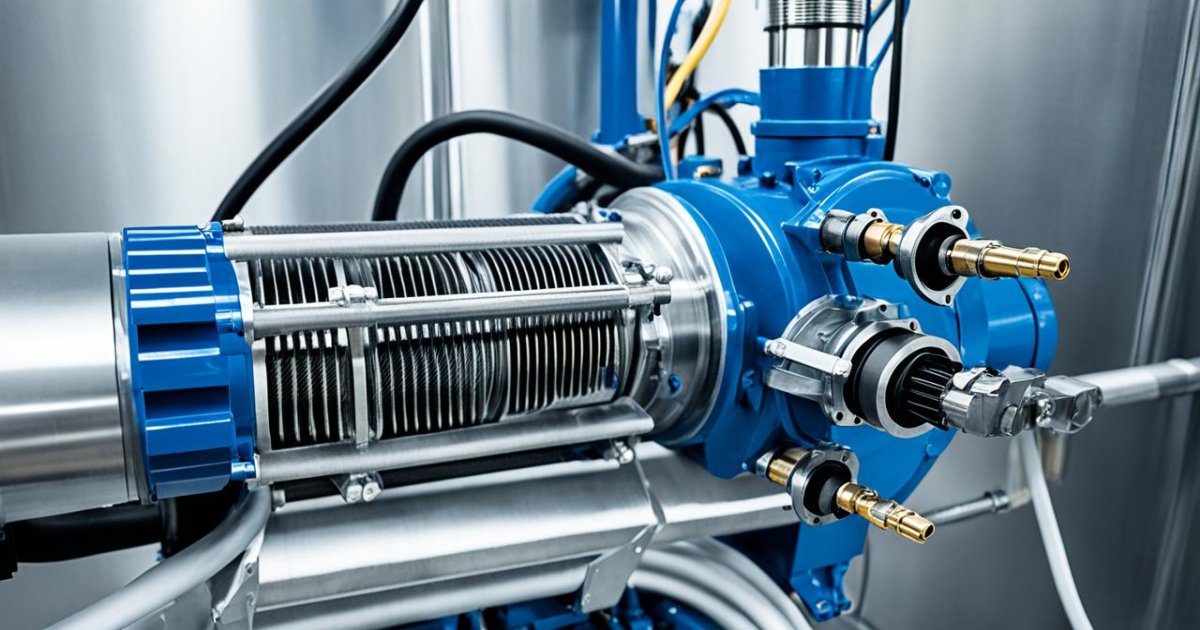
Key Takeaways
- Hydraulic system failures in freeze dryers can lead to big problems, causing lost productivity and issues with product quality.
- It’s important to understand how hydraulic systems work in freeze drying and what can go wrong to keep your equipment running well.
- Common reasons for hydraulic system failures include pump and valve issues, temperature problems, and vacuum sealing issues.
- Using preventative maintenance and good troubleshooting can help avoid hydraulic system failures and keep freeze drying smooth.
- Deciding when to replace or fix a hydraulic system is key to solving problems in freeze dryers.
Understanding the Importance of Hydraulic Systems in Freeze Dryers
Hydraulic systems are key to making freeze dryers work right. They control the temperature, pressure, and vacuum needed for freeze drying. If these systems don’t work, it can mess up the drying process big time. This includes problems with temperature control, vacuum sealing, and even breaking down the freeze dryer itself.
The Role of Hydraulic Systems in Lyophilization
Hydraulic systems keep the temperature and pressure in check during freeze drying. They make sure the product dries out right, which is key for keeping the product good and stable. If the hydraulic system has problems, it can mess up the drying process. This might lead to bad product quality or even losing an entire batch.
Potential Consequences of Hydraulic System Failure
- Temperature control issues, resulting in uneven or inadequate drying
- Vacuum sealing problems, leading to air infiltration and compromised product integrity
- Lyophilization process breakdown, causing significant delays and production losses
- Increased risk of equipment damage and the need for costly repairs or replacement
Knowing how important hydraulic systems are in freeze dryers is key to keeping things running smoothly. Fixing problems early and keeping up with maintenance helps make sure the drying process goes well. This leads to making high-quality products.
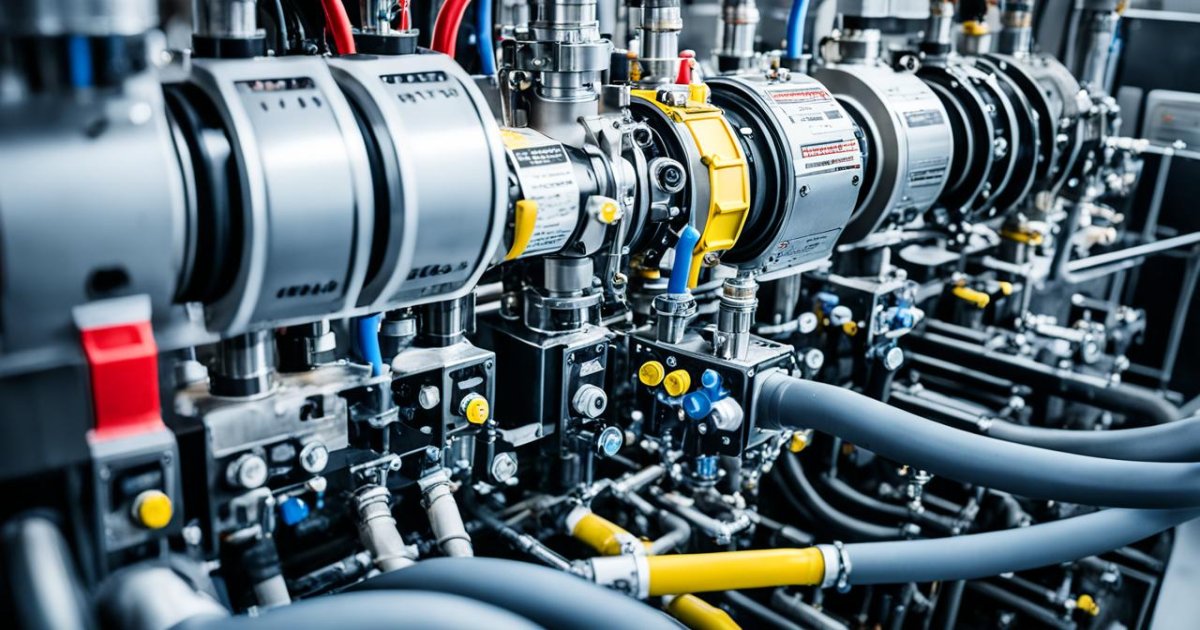
Common Causes of Hydraulic System Failure in Freeze Dryers
Freeze dryer hydraulic systems can face many issues that lead to failures. It’s key to find and fix these problems to keep freeze-drying equipment running smoothly. Some common causes of hydraulic system failure include:
Failure Hydraulic-pump
The hydraulic pump is vital for the freeze dryer. It makes sure the system has enough flow and pressure. If it fails, it might not work right, leading to a big problem.
Hydraulic Pump Failures: Pumps can break down due to wear, contamination, or not being maintained correctly. This leads to system breakdowns.
This message is given when the motor contactor for the hydraulic pump is activated, but there is no report that the pump is on. The causes of this failure could be:
- The corresponding motor protection switch has cut out and switched off the pump.
- The coil of the motor contactor is defective
- The control wire to the motor contactor has been interrupted
Failure of a hydraulic valve
Valves control the hydraulic fluid flow in freeze dryers. If they stick, leak, or don’t work, it can mess up the system. This can cause uneven pressure and flow issues, or even make the whole system stop working.
Valve Malfunctions: If valves are faulty or clogged, they can mess up the flow of hydraulic fluid. This causes system parts to fail. This failure message appears if a hydraulic valve is too long switched on:
- A door bolt doesn’t reach the limit
- A door drive doesn’t reach the limit
- The chamber/condenser valve doesn’t reach the limit
- The shelf system doesn’t reach the limit switch.
Fixing failure hydraulic pump and failure of a hydraulic valve issues are key to getting the freeze dryer working again. Quick repairs or maintenance are needed to keep it running well.
Knowing about system component failures in freeze dryer hydraulic systems helps technicians fix problems fast. This cuts down on downtime and keeps the freeze drying process running smoothly.
Hydraulic oil excess temperature
Freeze-drying faces big challenges with temperature control problems. These issues can mess up the balance needed for successful drying. This can lead to bad results and even break the equipment.
Fixing temperature control problems is vital for avoiding hydraulic system failures. It also keeps the freeze-drying equipment running smoothly. Regular checks and keeping an eye on the temperature can prevent these issues. This ensures the freeze dryer works well and reliably.
Temperature Control Issues: Temperature changes can change hydraulic fluid’s viscosity. This affects how well the system works. This failure message appears when the excess temperature safety switch has switched off the hydraulic pump The hydraulic pump is switched on automatically again after a cooling-down period. The causes of this failure could be: the hydraulic pump was running to long.
- Delay: No
- Auto-return: yes
level hydraulic oil is low
Vacuum Sealing Problems: Air getting into the vacuum system can cause pressure and fluid flow issues. This failure message appears when the level switch reports a low level of hydraulic oil. The cause of this failure could be a leak in the hydraulic system.
- Delay: No
- Auto-return: yes
Filter hydraulic polluted or contaminated
This failure message appears when the differential pressure switch reports high pressure at the hydraulic oil filter. The causes of this failure could be: the hydraulic oil filter is polluted or contaminated because of dirty hydraulic oil.
These problems can come from many things, like worn-out parts, dirty fluids, and not following maintenance steps. By finding and fixing the main causes of hydraulic system failures, freeze drying operators can keep their equipment running well and efficiently.
Troubleshooting and Repair Guidelines for Hydraulic Systems
Keeping your freeze drying equipment running well means understanding the hydraulic system and its parts. If you face system failures, it’s key to troubleshoot and repair with a clear plan. This helps find and fix the main problem.
Diagnostic Tools and Techniques
To start fixing a hydraulic system failure in your freeze dryer, use special tools and methods. Watch the system’s pressures, temperatures, and fluid conditions. This helps you find the problem and plan a good repair.
- Use pressure gauges to check pressures in the hydraulic system. Look for any odd pressure changes or drops that could mean a part is broken.
- Keep an eye on the hydraulic fluid’s temperature. It should stay within the range the maker suggests. High temperatures can cause parts to wear out too fast and fail.
- Check the hydraulic fluid often for dirt, color changes, or signs it’s breaking down. If you find any, you might need to change the fluid or clean the system.
Conclusion
Freeze drying equipment relies heavily on a well-working hydraulic system. Knowing how to fix common issues like pump and valve problems is key. It also includes managing temperature and ensuring the vacuum seal is tight.
Regular maintenance is crucial to avoid hydraulic system failures. This means checking the equipment often, keeping an eye on the hydraulic fluid, and replacing or upgrading parts when needed. These steps help keep freezer dryers running smoothly.
Fixing hydraulic system problems requires careful troubleshooting and the right tools. Freeze drying experts should be proactive to avoid issues. By doing so, they can keep their operations running smoothly and ensure top-quality products.
FAQ
What are the common causes of hydraulic system failures in freeze dryers?
Common causes include hydraulic pump failures, valve malfunctions, and temperature control issues. These can stem from wear and tear, fluid contamination, and poor maintenance.
How can hydraulic pump failures affect the freeze-drying process?
Pump failures can reduce flow or pressure, affecting the freeze-drying process. It’s important to fix or replace pumps to keep the system working right.
What can cause valve malfunctions in freeze dryer hydraulic systems?
Valves can get stuck, leak, or not work right, affecting the system’s flow and control. Fixing or replacing these valves is key to keeping the freezer dryer reliable.
How can temperature control issues impact the hydraulic system in a freeze dryer?
Bad temperature control can cause the hydraulic oil to get too hot, harming the system. Fixing temperature issues and managing the fluid well are crucial to avoiding failures and keeping the freezer dryer efficient.
What are the potential consequences of vacuum sealing problems in a freeze dryer?
Vacuum leaks or pump issues can mess with the pressure, affecting the hydraulic system. Fixing vacuum problems is vital for the freeze dryer’s integrity and avoiding system failures.
How can preventative maintenance strategies help address hydraulic system failures in freeze dryers?
Regular checks, cleanings, and fluid management can spot and fix problems early. This approach lowers the chance of sudden failures and keeps the freeze-drying process smooth.
What are some key equipment maintenance protocols for freeze dryer hydraulic systems?
Key protocols include regular checks for wear or dirt, cleaning parts, and keeping an eye on the fluid’s temperature, level, and cleanliness. These steps prevent many common failures.
When should users consider component replacement or equipment upgrades for their freeze dryer hydraulic systems?
Replace worn or broken parts like pumps, valves, or seals to fix the system. Upgrading with better components can also boost the freeze dryer’s performance and life.
What are some key troubleshooting and repair guidelines for addressing hydraulic system failures in freeze dryers?
Use tools and techniques to find the problem, like checking pressures, temperatures, and fluid conditions. Then, decide if repairs or replacements are needed to get the system back to normal.