Defrosting Procedure of Freeze Dryer: A Comprehensive Guide
Freeze drying, or lyophilization, is a process used to preserve a wide range of products by removing moisture through sublimation. This method is vital in various industries, including pharmaceuticals, food processing, and biotechnology. An essential part of maintaining and operating a freeze dryer is the defrosting procedure, which ensures the equipment remains efficient and effective. In this article, we’ll delve into the defrosting procedure of a freeze dryer, exploring each step in detail to provide a thorough understanding.
This guide will walk you through defrosting a freezer dryer step by step. It’s for both newbies and experts in lyophilization. You’ll learn how to keep your freezer dryer working at its best.
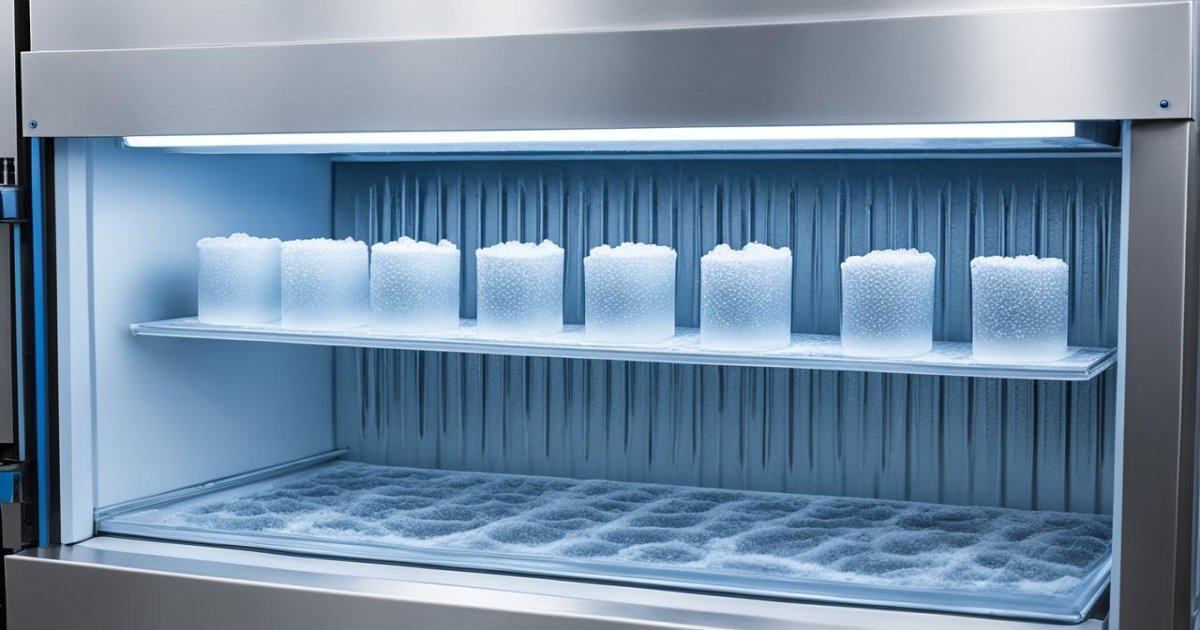
Key Takeaways
- Defrosting is vital for keeping freeze dryers efficient and working right. It stops ice from building up and saves time.
- Correct defrosting and upkeep help freeze dryers last longer and avoid mechanical problems.
- Auto-defrosting in recipes makes freeze-drying easier, leading to better results and more efficiency.
- You need the right utilities, like compressed air, chilled water, clean steam, and nitrogen, for defrosting.
- Follow safety rules, like not using extension cords and keeping kids away from the freezer, to stay safe.
What is freeze-drying?
Definition and Purpose of freeze-drying
Freeze drying, or lyophilization, is a dehydration process typically used to preserve perishable materials. The process works by freezing the product and then reducing the surrounding pressure to allow the frozen water in the material to sublimate directly from the solid phase to the gas phase.
Industries that Utilize Freeze Drying
Industries that commonly use freeze drying include pharmaceuticals for preserving vaccines and other medications, food processing for producing lightweight, long-lasting food items, and biotechnology for preserving biological samples.
Importance of defrosting a freeze dryer
Efficiency and Performance: Defrosting a freeze dryer is crucial for maintaining its efficiency and performance. Ice buildup on the condenser can impede the machine’s ability to function correctly, leading to longer processing times and potential damage.
Preventing Equipment Damage
Frequent defrosting keeps too much ice from forming, which can shorten the equipment’s lifespan and lead to mechanical problems. Proper maintenance ensures the longevity and reliability of the freeze dryer.
Description of the Defrosting Procedure
General Overview
The freeze dryer defrosting procedure is key to keeping the equipment running well. It removes ice or frost that builds up, ensuring the freeze dryer works right and avoids problems.
Freeze dryers can defrost manually or automatically, depending on the model. It’s important to take out any product before defrosting starts.
The defrosting procedure involves several steps that must be followed to ensure the freeze dryer is adequately maintained. This process can be performed manually or automatically, depending on the equipment’s capabilities.
Key Steps Involved
- Unloading the Product.
- Checking Utility Requirements.
- Setting Parameters.
- Starting the defrosting cycle.
- Monitoring the process.
- Verifying Completion.
Checks and Precautions Before Defrosting
Before defrosting, check if you have clean steam and that all valves are set right. This makes defrosting go smoothly and avoids issues.
Look over the freeze dryer and its parts to see what needs extra care during defrosting. This helps avoid damage and makes sure defrosting works well
The time it takes to defrost depends on how much frost there is. Light frost takes 2-3 hours, moderate frost takes 4-5 hours, and heavy frost takes 6–8 hours.
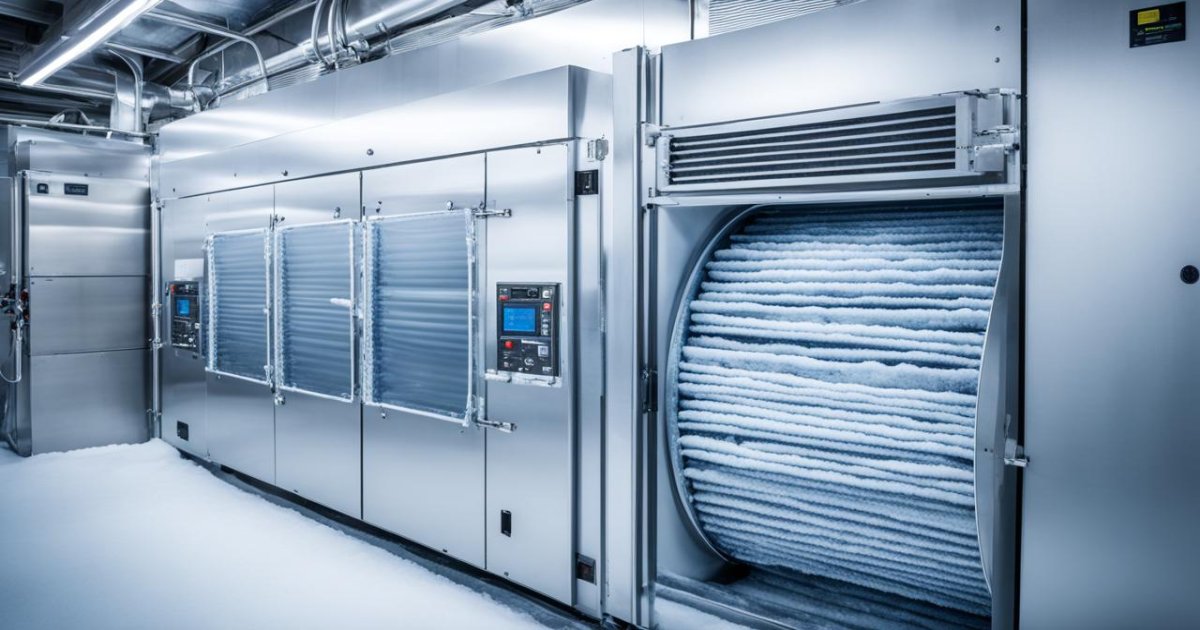
Unloading the Product
Ensure the product is unloaded from the chamber of the freeze dryer before starting the defrosting cycle. This step is critical to preventing contamination and damage to the product.
Auto-defrosting in Recipes
If auto-defrosting is selected in the freeze-drying recipe, the condenser automatically gets defrosted during unloading. This feature guarantees consistent outcomes while streamlining the procedure. Here are five important points related to “auto-defrosting in recipes.”
- Automatic Condenser Defrosting: When auto-defrosting is selected in the freeze-drying recipe, the condenser defrosts automatically during the unloading process, eliminating the need for manual defrosting.
- Consistent Results: Auto-defrosting ensures that each batch is processed under the same conditions, leading to consistent and reliable outcomes across multiple freeze-drying cycles.
- Streamlined Workflow: By automating the defrosting process, auto-defrosting streamlines the freeze-drying procedure, reducing downtime and increasing overall efficiency.
- Reduced Labor: This feature minimizes the need for manual intervention, freeing up personnel to focus on other critical tasks and improving operational productivity.
- Enhanced Equipment Longevity: Regular and automatic defrosting prevents ice buildup in the condenser, reducing wear and tear on the equipment and potentially extending its lifespan.
Ensuring Clean Steam Availability
Check the SCADA (Supervisory Control and Data Acquisition) system’s steam supply indication to make sure clean steam is available. Effective defrosting requires clean steam. Here are six important points related to Ensuring Clean Steam Availability
- SCADA System Monitoring: Regularly check the SCADA system’s steam supply indication to ensure clean steam is available, which is crucial for maintaining process integrity.
- Effective Defrosting: Clean steam is essential for effective defrosting in freeze-drying processes, ensuring that equipment operates efficiently and without contamination.
- Preventing Contamination: Ensuring the availability of clean steam prevents contamination of the product, maintaining the quality and safety of pharmaceutical preparations.
- Consistent Performance: Reliable access to clean steam ensures consistent performance of the freeze-drying equipment, leading to uniform results across different batches.
- Maintenance and Inspections: Regular maintenance and inspections of the steam supply system help identify and address issues promptly, ensuring a continuous supply of clean steam.
- Operational Efficiency: Ensuring clean steam availability optimizes the overall operational efficiency of the freeze-drying process, reducing downtime and enhancing productivity.
- Analyze the Sample: Analyze the collected steam sample for quality parameters such as steam dryness, non-condensable gases, and superheat. Use appropriate methods and equipment for analysis
The steam dryness level needs to be at least 0.95, meaning 95% steam and 5% water. For laboratory autoclaves, a dryness level as low as 90% is still okay. If the steam is less than 90% dry, it is considered wet steam and not acceptable.
Initial Valve States
Ensure that the main isolation valve is closed and all valves are in their normal state before beginning the defrosting cycle. This precaution helps maintain system integrity.
Utility Requirements for Defrosting
Compressed Air
Make sure compressed air is supplied at a minimum pressure of 0.4 MPa. Compressed air is necessary for various pneumatic functions during the defrosting process.
Chilled Water
Chilled water should be available at not less than 1.0 kg/cm2. This utility is crucial for cooling and maintaining appropriate temperatures during defrosting.
Clean Steam
Clean steam must be available ata pressure of not less than 0.3 MPa. Steam plays a vital role in the defrosting process by providing the necessary heat.
Nitrogen
Ensure nitrogen is available at not less than 0.3 MPa. Nitrogen is often used for venting and purging during the defrosting cycle.
Utility | Requirement |
---|---|
Compressed Air | Necessary for various pneumatic components and controls |
Chilled Water | Required for the condenser and refrigeration system cooling |
Clean Steam | Used for temperature-controlled, heated shelves during defrosting |
Nitrogen | Utilized for product chamber pressurization and inert atmosphere |
Pre-Defrosting Checks
Healthy Condition Verification
Before starting the defrosting cycle, check that all start conditions are in a healthy state. This verification includes ensuring all systems and components are functioning correctly.
Equipment Readiness
Confirm that the freeze dryer is ready for the defrosting cycle. This readiness involves verifying that all parameters are set correctly and utilities are available.
Frequency of Defrosting
Post-Freeze-Drying Cycle
Defrosting of the freeze dryer condenser should occur after the completion of each freeze-drying cycle. Regular defrosting helps maintain optimal performance.
Periodic Performance Verification (PPV) and Requalification (RQ) Runs
In cases of periodic performance verification (PPV) or requalification (RQ) runs, or as per scheduled qualifications, a defrosting cycle should be performed. These runs ensure the freeze dryer operates within specified parameters.
Detailed Procedure for Defrosting Process
Auto-Mode Procedure
The auto-mode procedure simplifies the defrosting process by automating many steps. Follow these guidelines for an efficient auto-mode defrosting cycle.
Auto-Mode Defrosting Steps
Parameter Setting
Set the parameters for the defrosting cycle on your freeze dryer SCADA system. These parameters include temperature, time, and pressure set points.
Starting the Cycle
Start the defrosting cycle by entering the correct username and password on the SCADA system. This step initiates the automated process.
Monitoring and Completion
Visually check the presence of ice on the condenser coil through the view glass during the auto-defrosting cycle. Ensure the completion of the defrosting cycle by verifying the “process finished” message on the main SCADA screen.
Parameter Settings for Defrosting
Temperature-Set Points
- Condenser Drain Temperature: 90 to 96 degrees Celsius
Time-Set Points
- Defrosting Time: 15 to 20 minutes
- Drying Time: 30 to 35 minutes
- Delayed After Steam Exhaust: 32 seconds
- TBA Drain Time: 15 minutes
Pressure-Set Points
- Lower Hysteresis of Steam Inlets: 12 Mbar
- Upper Hysteresis of Steam Inlets: 26 Mbar
Additional Functions During Defrosting
Venting Gas Options
Use nitrogen or air for venting gas during the defrosting process. These gases help maintain appropriate pressure and prevent contamination.
Situational Uses
- Nitrogen: Best for high-stakes environments where contamination must be avoided.
- Air (compressed air): suitable for less critical applications where cost is a concern.
Visual Inspection During Defrosting
Monitoring Ice Presence
Check for the presence of ice on the condenser coil through the view glass. This visual inspection ensures the defrosting process is proceeding correctly.
Ensuring Cycle Completion
Verify the completion of the defrosting cycle by confirming the “process finished” message on the SCADA screen. This step ensures the cycle has concluded successfully.
Post-Defrosting Verification
Batch Report Verification: Verify the batch report of the defrosting process (DFR). This report provides detailed information about the cycle and confirms its successful completion.
Conclusion
Defrosting a freezer dryer is a critical maintenance task that ensures the equipment remains efficient and reliable. By following the outlined steps and precautions, operators can effectively defrost their freeze dryers, maintaining optimal performance and extending the lifespan of their equipment. Regular defrosting, along with periodic checks and maintenance, helps prevent issues and ensures consistent results in freeze-drying processes.
FAQs
Why is defrosting a freezer dryer important?
Defrosting is essential to maintaining the efficiency and performance of the freeze dryer by preventing ice buildup, which can cause mechanical issues and reduce processing efficiency.
How often should I defrost my freezer dryer?
Defrosting should be performed after each freeze-drying cycle and during periodic performance verification or requalification runs.
What are the key utilities required for defrosting a freezer dryer?
Key utilities include compressed air, chilled water, clean steam, and nitrogen, each playing a vital role in the defrosting process.
Can defrosting be automated in a freezer dryer?
Yes, many modern freeze dryers offer an auto-mode defrosting procedure, which simplifies the process by automating various steps.
What should I do if ice remains on the condenser after defrosting?
If ice remains, verify that all parameters and utilities are set correctly. Repeat the defrosting cycle if necessary, and ensure no underlying issues are causing incomplete defrosting.