Vacuum Pump Failure in Freeze Drying: What to Know
Did you know a single vacuum pump failure can cost up to $1 million and cause delays in production? This shows how important it is to understand and prevent these issues. As a pharmaceutical professional, you must be aware of the risks.
This article will cover the challenges of vacuum pump failure in freeze drying. We’ll look at why these failures happen, their effects, and how to prevent them. This will help keep your freeze dry
Key Takeaways
- Vacuum pump failure during freeze drying can lead to significant product losses and production delays.
- Understanding the role of vacuum pumps in the freeze-drying process is essential for maintaining smooth operations.
- Common causes of vacuum pump failure include motor protection switch issues and defective motor contactor coils.
- Proper troubleshooting and preventive maintenance strategies are crucial to mitigating the risk of vacuum pump malfunctions.
- Implementing robust quality control and monitoring protocols can help detect and address vacuum pump issues before they disrupt the freeze-drying process.
Understanding Freeze Drying and Vacuum Pumps
Freeze drying, also known as lyophilization, is a key method in the pharmaceutical world. It keeps delicate active pharmaceutical ingredients (APIs) and biologics stable and potent. Vacuum pumps are crucial here. They create the low-pressure needed for water to change directly from solid to gas.
The Importance of Vacuum Pumps in the Freeze-Drying Process
Vacuum pumps are key to freeze drying. They remove moisture from the frozen product. This low-pressure lets water turn directly from solid to gas. This keeps the product’s structure and effectiveness intact.
How Vacuum Pumps Operate in Lyophilization Cycles
Vacuum pumps are vital at every stage of lyophilization. In freezing, they lower pressure so water freezes. During drying, they keep the pressure low for ice to turn directly into vapor. In the final stage, they help get rid of any leftover moisture, keeping the product fresh longer.
Stage of Lyophilization Cycle | Role of Vacuum Pump |
---|---|
Freezing | Lowers pressure to allow water to freeze |
Primary Drying | Maintains low-pressure environment to facilitate sublimation |
Secondary Drying | Supports removal of residual moisture |
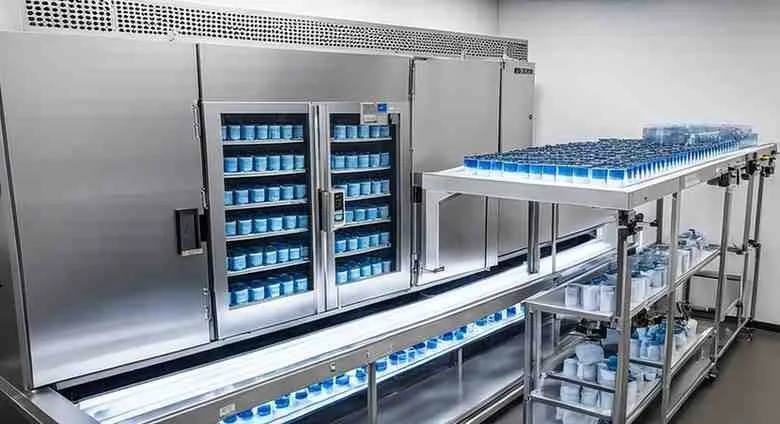
“Vacuum pumps are the heart of the freeze drying process, ensuring the successful preservation of sensitive pharmaceutical products.”
Common Causes of Vacuum Pump Failure
Vacuum pumps are key in freeze drying, but they can face problems that lead to failure. Issues like motor protection switch problems and motor contactor coil defects are common.
Motor Protection Switch Issues
Motor protection switches protect the vacuum pump’s motor from overloads and short circuits. But if they don’t work right, they can turn off the pump. This can be caused by power surges, wiring issues, or ice or debris around the switch.
Defective Motor Contactor Coils
The motor contactor coils help start the vacuum pump’s motor. If they’re damaged, the pump might not start or run right. This damage can come from wear and tear, too much heat or moisture, or other environmental factors.
Fixing these common vacuum pump problems is key to keeping freeze drying working well. By knowing these issues and checking the pump often, you can avoid problems and keep your freeze-drying process smooth.
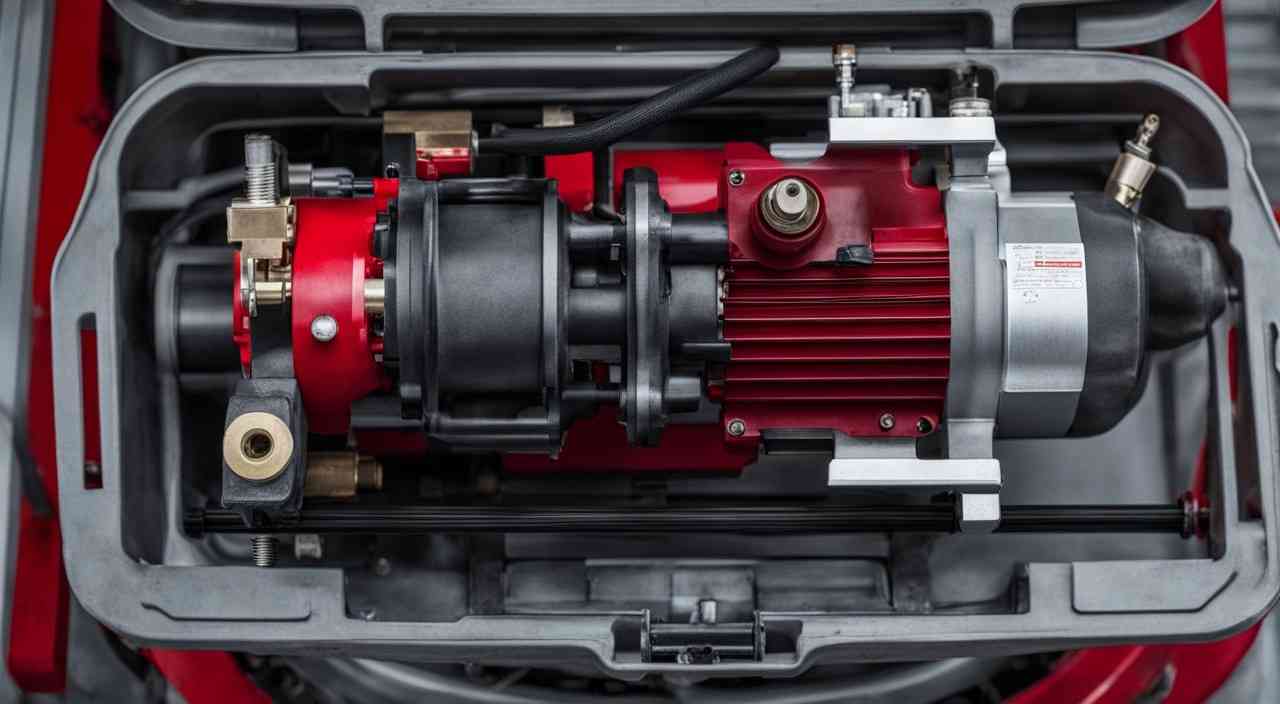
Troubleshooting Vacuum Pump Malfunctions
When a vacuum pump fails during freeze drying, it’s key to find and fix the problem fast. This guide will walk you through how to diagnose and fix vacuum pump issues. It aims to keep your lyophilization cycles running smoothly.
Start by checking the system for any blockages in the vacuum lines. Make sure all connections are tight and airtight. Also, look at the pump’s motor and cooling system for any damage or wear.
- Check the vacuum pump’s motor protection switch. If the switch has tripped, it may indicate an issue with the motor or a power supply problem.
- Inspect the motor contactor coils for any defects. Faulty coils can prevent the vacuum pump from starting or running properly.
- Verify that the cooling system is functioning correctly. Disruptions in the cooling medium or issues with the cooling system can lead to vacuum pump failures.
If the problem still exists after these checks, you might need a professional to help. Getting your vacuum pump fixed quickly can save you from costly delays and ensure your freeze drying goes well.
Troubleshooting Step | Potential Issue | Recommended Action |
---|---|---|
Check motor protection switch | Motor or power supply problem | Reset or replace the switch if necessary |
Inspect motor contactor coils | Defective coils | Replace the faulty contactor coils |
Verify cooling system operation | Cooling system disruption | Troubleshoot and repair the cooling system |
Quick and detailed troubleshooting of vacuum pump issues is crucial. It keeps your freeze-drying process reliable and your products top quality.
Failure of an Active Vacuum Pump During Freeze Drying
When an active vacuum pump fails during freeze drying, it can cause big problems. It disrupts the lyophilization cycle and might affect the product’s quality. It’s important to find out why the pump failed and fix the issue to keep freeze drying going smoothly.
Identifying the Root Cause
First, we need to figure out why the vacuum pump stopped working. This means looking closely at the pump’s performance and the control systems. We also check the freeze-drying equipment. Important things to look at include:
- Any issues with the motor protection switch that may have led to the pump’s shutdown
- Potential problems with the motor contactor coils could have caused the pump to malfunction
- Disruptions in the control lines that regulate the vacuum pump’s operation
Addressing Control Line Interruptions
Control lines often get interrupted, which can make the vacuum pump fail. These lines are key for keeping the pump running right. To fix this, we should:
- Check the control lines for any damage or loose connections
- Make sure the control lines are grounded and shielded to avoid interference
- Check that the control system is working correctly and sending the pump the right signals
By finding and fixing the root cause and any control line issues, we can get the active vacuum pump working again. This way, we can keep freeze drying going with little impact on product quality.
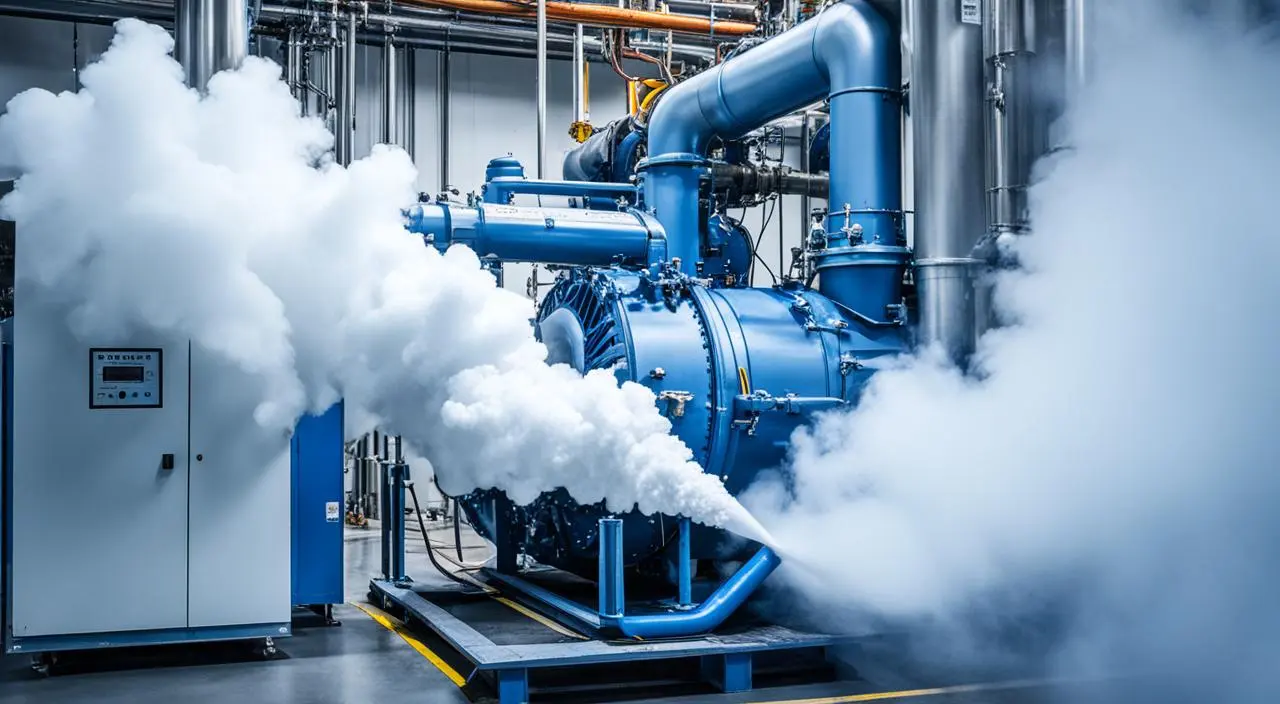
Temperature-Related Vacuum Pump Failures
Vacuum pump failures can be a big problem in freeze drying. Temperature issues are often the main cause. These come from cooling system problems or not having enough cooling medium. This can cause big issues with your vacuum pumps.
Cooling System Disruptions
Keeping vacuum pumps cool is key for freeze drying. If the cooling system breaks down, like a bad chiller or blocked lines, pumps can get too hot. This leads to wear and tear, less performance, and even pump failure.
Lack of Cooling Medium
Not having enough cooling medium, like water or refrigerant, is another big problem. Without enough, pumps can’t cool down during use. This causes overheating and damage.
To stop and fix these pump failures, keep your cooling system strong. Check the cooling medium often and do regular maintenance. By being careful and fixing these issues, you can keep your vacuum pumps working well during freeze drying.
“Proper temperature control is the key to maintaining the optimal performance and longevity of your vacuum pumps during freeze drying.”
Impact on the Freeze-Drying Process
If a vacuum pump fails during freeze drying, it can greatly affect the process and the final product. The main worries are about the vacuum level and the quality of the product.
Vacuum Level Disruptions
Vacuum pumps are key to keeping the pressure low for freeze drying to work well. If a pump fails, the vacuum level can drop or disappear. This messes up the freeze drying, slows down drying, and makes it hard to remove moisture.
Potential Product Quality Issues
Loss of vacuum during freeze drying can cause big problems with the final product. It might not dry completely, have uneven moisture, and change its physical and chemical makeup. These issues can affect how long the product lasts, its shelf life, and how well it works.
To lessen the effects of vacuum pump failures, having a strong backup plan is key. This includes having extra vacuum systems, regular maintenance, and checks to spot and fix vacuum level issues fast.
Knowing how important vacuum pumps are in freeze drying helps you deal with problems early. This way, you can keep your freeze-dried products top-quality and safe.
Preventive Maintenance Strategies
Keeping your freeze drying equipment in top shape is key to smooth production. Using preventive maintenance strategies for your vacuum pumps and other important parts helps avoid big problems during the freeze drying process.
Regular checks are a big part of a strong maintenance plan. Look over your vacuum pumps and other systems for any signs of wear or damage. This way, you can fix small issues before they turn into big ones.
A good preventive maintenance plan also includes:
- Cleaning all parts to stop dirt and contaminants from building up
- Replacing important parts like seals, bearings, and filters when needed, as the maker suggests
- Watching key signs like vacuum levels and energy use helps spot any problems early
Putting effort into preventive maintenance helps your freeze drying equipment work well and cuts down on unexpected downtime. This keeps your final products consistent and high quality.
“Proactive maintenance is the key to maximizing the performance and lifespan of your freeze drying equipment.”
Quality Control and Monitoring Protocols
Keeping your freeze drying operations in top shape means being proactive with quality control and monitoring. Along with regular maintenance, strong quality control steps and monitoring can catch vacuum pump problems early. This prevents process issues and keeps product quality high.
Checking your vacuum pumps often is key to quality control. Look for wear or damage, track performance, and do regular maintenance. This way, you can fix problems fast and avoid downtime. It also keeps your freeze-dried products top-notch.
Checking the freeze drying process in real-time is also vital. Use sensors, data loggers, and analytics to watch vacuum levels, temperature, and moisture. This lets you spot and fix any pump or process issues quickly.
Quality Control Measure | Monitoring Protocols |
---|---|
|
|
A detailed quality control and monitoring program keeps you ahead of vacuum pump problems. It ensures your freeze drying works well and consistently. This proactive method not only safeguards your products but also boosts your process efficiency and productivity.
“Effective quality control and monitoring are the cornerstones of a robust freeze drying operation. By staying vigilant and addressing issues promptly, you can ensure the reliability and consistency of your process.”
Contingency Planning for Vacuum Pump Failures
Unexpected vacuum pump failures can disrupt the freeze drying process. This can lead to big problems for your business. It’s key to have a solid contingency plan to keep things running smoothly. This guide will help you make a plan with backup systems, alternative equipment, and response steps for vacuum pump failures.
Backup Systems and Redundancy
Having a reliable backup system is crucial for a good contingency plan. Think about getting a second vacuum pump for backup. This pump should be ready to take over if the main one fails. Make sure to test and keep the backup in good shape.
Alternative Equipment and Suppliers
Find and connect with suppliers who can quickly provide new vacuum pumps or parts. This can cut down on downtime and keep your freeze drying going. Always check and update your list of suppliers to make sure they’re ready and quick to respond.
Documented Response Protocols
Make clear, step-by-step plans for what to do if a vacuum pump fails. These plans should include how to safely shut down and handle materials. Make sure all your team knows these plans well to be ready for anything.
Contingency Planning Strategies | Benefits |
---|---|
Backup Vacuum Pump System | Ensures continuous operation during primary pump failures |
Alternative Supplier Relationships | Expedites access to replacement pumps or components |
Documented Response Protocols | Provides clear guidance for efficient recovery from failures |
Using these strategies for contingency planning helps protect your freeze drying work. Being proactive and prepared is key to keeping your business going and ensuring your products are top quality.
“Effective contingency planning is the key to weathering the storm of unexpected equipment failures in the freeze drying process.”
Conclusion
In the world of making medicines, freeze drying is a key step that needs perfect precision. The vacuum pump is a crucial part of this process. If it fails, it can greatly affect the quality of the product and how well the production runs. Knowing why vacuum pumps fail helps you fix these problems and make your freeze drying better.
Causes of vacuum pump failures include things like motor switch problems and bad motor contactor coils. To avoid these issues, you should do regular maintenance and check the quality of your pumps. Also, keep an eye on them and fix any problems early to stop them from messing up your freeze drying.
If a vacuum pump fails during freeze drying, it can cause big problems. It can affect the quality of the product. So, it’s important to find out why it failed and fix it fast. Having a good plan for when things go wrong helps you keep your production running smoothly.
Dealing with vacuum pump failures can make your freeze drying process better, improve pharmaceutical manufacturing, and make sure your products are always of top quality. By doing regular maintenance, checking quality, and planning for emergencies, you can avoid the risks of vacuum pump failure and process optimization.
“Proactive management of vacuum pump failures is essential for maintaining the integrity of the freeze drying process and ensuring the consistent production of high-quality pharmaceutical products.”
Additional Resources
For more info on handling vacuum pump failures in freeze drying, check out these trusted websites and top sources:
The International Society for Lyophilization and Freeze Drying (ISLD) has a great resource library. It includes technical guides, case studies, and best practices for vacuum pump issues in pharmaceuticals. Visit www.isld.org for more.
The Parenteral Drug Association (PDA) offers lots of resources on freeze drying and equipment. This includes troubleshooting tips and maintenance for vacuum pumps. Start your search at www.pda.org.
The U.S. Food and Drug Administration (FDA) has guides and rules on vacuum pumps for freeze drying in pharmaceuticals. You can find these at www.fda.gov.
FAQ
What are the common causes of vacuum pump failure during the freeze-drying process?
Vacuum pump failures often happen when motor protection switches turn off the pump. Another reason is when the motor contactor coils don’t work right, stopping the pump from starting.
How can I troubleshoot a vacuum pump malfunction during freeze drying?
First, find out why the pump stopped working. Check the control lines for any problems. Also, look for temperature issues, like cooling system failures or no cooling medium.
How can vacuum pump failures impact the freeze-drying process?
If a vacuum pump fails, it can mess with the vacuum level. This affects the quality of the final product. It can change the product’s stability, potency, and other important features.
What preventive maintenance strategies can I implement to minimize the risk of vacuum pump failures?
To prevent pump failures, regularly check, clean, and replace important parts. This keeps your vacuum pumps and freeze drying gear working well.
How can I develop a contingency plan for addressing vacuum pump failures during the freeze-drying process?
Make a detailed plan with backup systems, other equipment, and clear steps to follow. This helps you handle pump failures better and keeps your freeze drying work running smoothly.